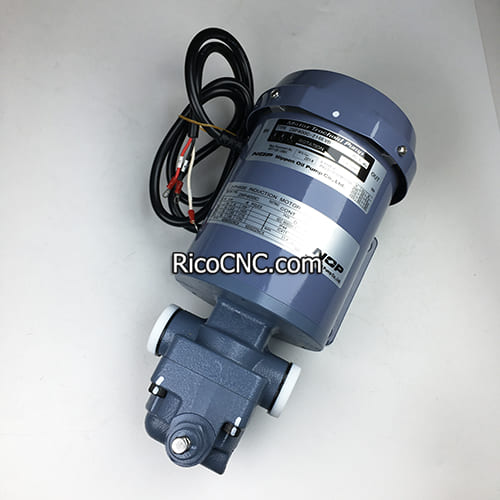
What is a Vane Pump?
A vane pump is a type of positive displacement pump that operates using vanes mounted to a rotor. These vanes slide in and out of slots to create pressure against the inner walls of a chamber, facilitating the movement of fluids. In the automation industry, vane pumps are renowned for their ability to provide a consistent flow and their efficiency in numerous applications, from hydraulic systems to automotive transmission.
Understanding the Basic Components of a Vane Pump
Vane pumps are primarily made up of the following components:
Rotor: The rotor is the central part of the vane pump where the vanes are installed. It rotates to create centrifugal force, which pushes the vanes outward.
Vanes: These sliding parts extend from the rotor to form a seal against the inner chamber wall. They play a crucial role in pumping the fluid.
Chamber: The chamber, also known as the casing, is where the fluid is collected, pressurized, and discharged.
The working mechanism of the vane pump is both elegant and simple. When the rotor turns, the centrifugal force causes the vanes to make contact with the chamber walls, creating pockets of fluid. As the rotor continues to spin, these pockets are compressed, generating pressure to move the fluid out through an outlet. This principle of operation is what makes vane pumps a type of positive displacement pump.
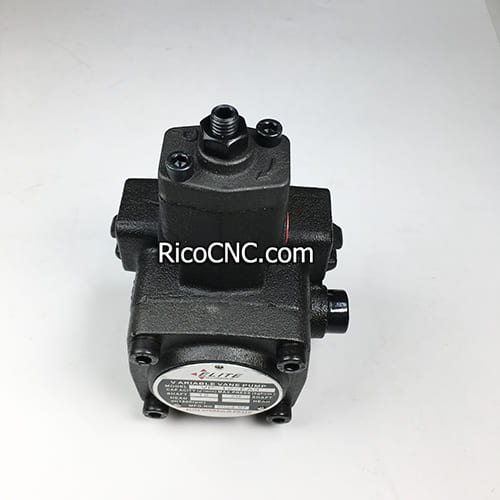
For more detailed specifications, check out our VP-12-FA3 Elite Low-Pressure Variable Vane Pump.
Types of Vane Pumps
There are several variations of vane pumps, each suited for different operational needs. Some common types include:
Rotary Vane Pumps: These are often used for hydraulic applications and are popular for their simple construction and reliability.
Sliding Vane Pumps: A subtype designed specifically for fluids with low viscosity, making them suitable for transporting fuels or oils.
Variable Displacement Pumps: These pumps have adjustable flow rates, allowing for versatile applications and efficient energy use.
The sliding vane pump is especially popular in the automation industry, offering high efficiency due to its adaptability to fluid viscosity and flow requirements.
For more information, read our guide on pump parts and their uses.
How Do Vane Pumps Work?
Vane pumps operate by converting mechanical energy into hydraulic energy. Here is a step-by-step breakdown:
Fluid Intake: As the rotor spins, the vanes extend out to form sealed compartments. The size of these compartments increases as they pass by the intake port, drawing fluid into the pump.
Compression Phase: When the rotor continues to spin, these sealed compartments get smaller, causing a compression effect that builds pressure in the fluid.
Fluid Discharge: Once compressed, the fluid exits through the outlet port, creating a steady flow rate that is crucial for applications needing precise control.
This positive displacement mechanism ensures a consistent output irrespective of pressure variations. Vane pumps are widely favored for their ability to maintain constant flow, making them an essential part of any hydraulic circuit.
For applications where consistent and reliable flow is crucial, vane pumps are the go-to choice, especially in automation systems that require precision.
Advantages of Vane Pumps
Vane pumps offer several advantages over other types of pumps:
Consistent Flow: Unlike centrifugal pumps, vane pumps provide a consistent flow rate, which is critical in hydraulic applications.
Versatility: They are adaptable to various fluids, including oils, fuel, and other low-viscosity liquids.
Efficiency: High efficiency is achieved because the vanes maintain continuous contact with the inner chamber wall, minimizing energy loss.
Some of the primary advantages of vane pumps include:
Lower Maintenance Requirements
Compact Design
Quiet Operation
Check out our range of pneumatic regulators that are commonly used alongside vane pumps to control the fluid pressure effectively.
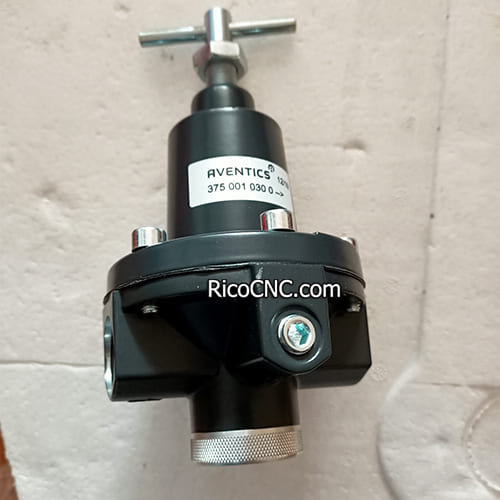
Applications of Vane Pumps in the Automation Industry
In the world of automation, vane pumps are integral components due to their flexibility and high efficiency. They are used in various applications, including:
Hydraulic Systems: Vane pumps are often used to generate fluid power in automated production lines.
Automotive Transmissions: Rotary vane pumps play an important role in maintaining pressure in transmission systems.
Lubrication Systems: These pumps are also widely used in machines for lubricating various parts, ensuring smooth operation.
The displacement pump capabilities of vane pumps make them suitable for handling a wide range of fluids, which is critical in industries like manufacturing and transport. Their ability to provide controlled fluid flow helps maintain a reliable automation system.
For more details on servo drives used in automation, explore our servo drive products.
Common Issues and Maintenance Tips for Vane Pumps
Like any mechanical system, vane pumps can experience some common issues, such as:
Vane Wear: Over time, vanes can wear out due to continuous contact with the chamber walls.
Cavitation: If not properly maintained, cavitation can occur, leading to damage inside the pump.
Overheating: Excessive fluid temperatures may result in reduced performance or potential damage to the pump.
To ensure a long operational life, it is important to conduct regular maintenance checks, such as:
Lubricating the Moving Parts: Lubrication helps in reducing friction between the vanes and the chamber walls, ensuring longer durability.
Checking for Contaminants: Regular inspections to ensure that the fluid is free from contaminants can prevent vane wear and maintain efficiency.
For proper maintenance tools, check out our sensor systems available here.
FAQs
1. What type of fluids can a vane pump handle?
Vane pumps are capable of handling a wide variety of fluids, including low viscosity fluids like fuel, oil, and even some chemicals. However, they are not ideal for pumping high viscosity fluids such as heavy grease.
2. How often should a vane pump be serviced?
Vane pumps should be serviced based on their operating conditions. For most industrial uses, a maintenance check every 3-6 months is recommended.
3. Can vane pumps be used in high-pressure systems?
Vane pumps are generally suitable for medium to low-pressure applications. For higher pressures, specialized pumps like gear pumps might be more appropriate.
4. What is the primary cause of vane pump failure?
The primary causes include vane wear, fluid contamination, and cavitation. Regular maintenance is key to preventing these issues.
5. What are some related components used with vane pumps?
Common components include servo drives, pneumatic regulators, and sensors for monitoring system performance. More details can be found in our related products section.
Conclusion
In conclusion, vane pumps are an indispensable part of many automated systems due to their reliability, consistent flow, and versatility. They provide an effective solution for applications needing precise pressure control and are well-suited for various fluids. With proper maintenance, these pumps can operate efficiently and contribute significantly to the smooth operation of automated systems.
If you need more insights or want to discuss how vane pumps can benefit your application, feel free to contact us. We are here to help you find the best solution for your automation needs.
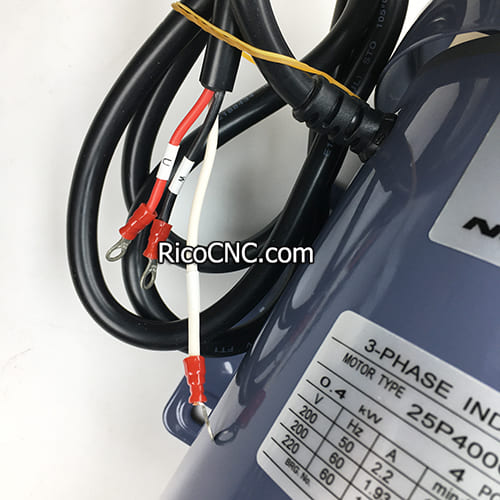