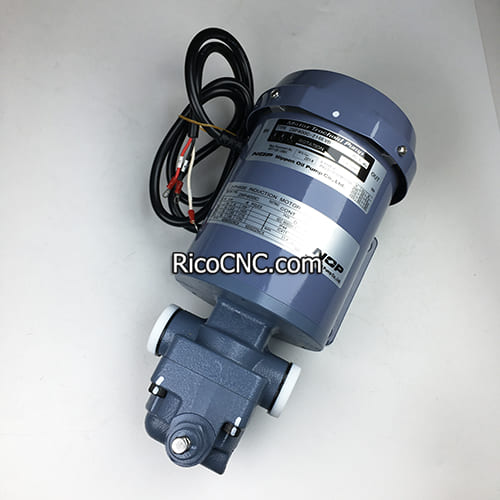
What is the Difference Between a Vane Pump and a Gear Pump?
Vane pumps and gear pumps are both common types of positive displacement pumps, often used in various industrial applications, including automation and manufacturing. While they share similarities, each pump type offers unique features that make them suitable for different applications. Understanding the distinctions between these two can help engineers and technicians make informed decisions regarding the best pump for their specific needs.
Overview of Vane Pumps and Gear Pumps
Vane Pumps are positive displacement pumps that use multiple sliding vanes mounted on a rotor to transport fluids. The vanes extend and retract as the rotor spins within a circular casing, creating fluid compartments that efficiently move the fluid from the inlet to the outlet. Vane pumps are often used in applications requiring a consistent flow rate and medium pressure.
On the other hand, Gear Pumps operate using a pair of rotating gears that mesh together to move fluid. Gear pumps have two types: external gear pumps and internal gear pumps. The gears create a suction effect as they rotate, trapping fluid between the gear teeth and moving it to the outlet. Gear pumps are highly valued for their durability and the ability to handle high-pressure fluids.
For more specific product details, check out our NOP Motor Trochoid Pumps, designed for effective fluid handling in various settings.
Working Mechanism of Vane Pumps
A vane pump works by utilizing a rotor with multiple vanes that slide in and out. When the rotor spins, centrifugal force pushes these vanes against the chamber wall, creating fluid compartments. As the rotor moves:
Fluid Intake: The volume between the vanes increases, creating a vacuum that draws fluid into the inlet port.
Compression Phase: The fluid is trapped between the vanes as the rotor continues to spin, compressing the fluid.
Fluid Discharge: The volume decreases as the vanes approach the outlet, forcing the fluid out of the pump.
This mechanism is beneficial for low to medium viscosity fluids and provides a consistent, reliable flow rate.
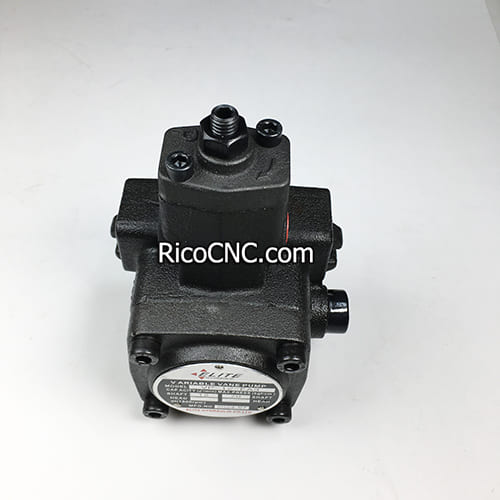
For more information on this type of pump, you can refer to our VP-12-FA3 Elite Low-Pressure Variable Vane Pump.
Working Mechanism of Gear Pumps
Gear pumps operate by using two or more rotating gears that mesh together. The gears create cavities that move the fluid through the pump in a positive displacement action.
External Gear Pumps: These pumps use two external gears that rotate in opposite directions. Fluid is trapped between the gear teeth and the casing and carried from the inlet to the outlet. These pumps are known for their durability and high-pressure capabilities.
Internal Gear Pumps: Internal gear pumps use an inner and an outer gear. Fluid is trapped in the space between the gears and moved through the system in a similar manner.
The gear teeth are responsible for trapping and transporting the fluid, making gear pumps ideal for high-pressure applications and fluids with varying viscosities.
Comparison of Vane Pumps vs. Gear Pumps
Feature | Vane Pump | Gear Pump |
---|---|---|
Mechanism | Sliding vanes on a rotor | Intermeshing gears (external or internal) |
Fluid Types | Best for low to medium viscosity | Suitable for a wide range of viscosities |
Pressure Capability | Medium pressure applications | High pressure capability |
Efficiency | Good at consistent flow with low noise | Very efficient, durable, can handle high pressure |
Maintenance | Vanes wear over time due to constant contact | Gears are generally more durable |
Applications of Vane Pumps
Vane pumps are commonly used in several specific applications due to their ability to handle low to medium pressure and their compact design. Typical uses include:
Fuel Transfer: Rotary vane pumps are often used for dispensing fuel due to their reliable flow rate.
HVAC Systems: Used to circulate refrigerants in HVAC systems, ensuring consistent pressure.
Lubrication Systems: Ideal for delivering low viscosity oils in lubrication applications.
In the automation industry, vane pumps are paired with systems like servo drives to maintain efficient flow control in dynamic environments.
Applications of Gear Pumps
Gear pumps excel in high-pressure environments and can manage fluids of varying viscosities, making them ideal for many challenging industrial applications:
Hydraulic Systems: Gear pumps are often used to generate the necessary pressure in hydraulic systems.
Chemical Processing: Able to handle high viscosity fluids, gear pumps are used in industries like chemical manufacturing.
Oil & Gas: Gear pumps are used to move heavy oils and other highly viscous liquids.
For industrial systems that require high pressure, gear pumps are a reliable choice. Consider exploring our servo motor solutions that can be paired with gear pumps for precision control.
Advantages and Disadvantages of Vane Pumps
Advantages
Consistent Flow: Vane pumps provide a consistent and predictable flow, ideal for applications needing steady pressure.
Compact Design: They are compact and lightweight, making them easy to install in tight spaces.
Quiet Operation: Vane pumps operate quietly, which is beneficial in environments where noise reduction is critical.
Disadvantages
Limited to Low Viscosity Fluids: They are not ideal for high viscosity fluids, which can cause vane sticking or reduced efficiency.
Wear and Tear: The sliding action of the vanes against the chamber wall results in mechanical wear over time, requiring regular maintenance.
Advantages and Disadvantages of Gear Pumps
Advantages
High Pressure Handling: Gear pumps are capable of managing high pressures, making them suitable for demanding applications.
Durable: With fewer moving parts subject to wear, gear pumps are often more durable compared to vane pumps.
Versatile Fluid Handling: Gear pumps can handle a wide range of fluid viscosities, making them versatile for different industries.
Disadvantages
Noise: Gear pumps tend to be noisier than vane pumps, especially in high-pressure settings.
Larger Footprint: They are often larger compared to vane pumps, making them less ideal for space-constrained environments.
How to Choose Between a Vane Pump and a Gear Pump
Choosing between a vane pump and a gear pump depends on your specific application needs:
Fluid Viscosity: For low viscosity fluids, a vane pump might be ideal. For higher viscosity fluids, gear pumps are better.
Pressure Requirements: For high-pressure needs, gear pumps are more suitable. Vane pumps are good for low to medium pressure.
Flow Requirements: If you need a consistent, steady flow rate, especially in automation settings, a vane pump might be the best choice.
For guidance on choosing the right pump, consider contacting our specialist team. We provide various pumps and automation solutions to meet diverse requirements.
FAQs
1. Which pump is more efficient for low viscosity fluids?
A vane pump is generally more efficient for handling low viscosity fluids as it ensures consistent flow without pulsation.
2. Can gear pumps handle high viscosity fluids?
Yes, gear pumps are specifically designed to manage high viscosity fluids, which makes them suitable for challenging fluids like heavy oils.
3. How often do vane pumps require maintenance?
Vane pumps need regular maintenance, typically every 3-6 months, to replace worn vanes and check for fluid contamination.
4. Are gear pumps noisy compared to vane pumps?
Yes, gear pumps can be noisier, especially in high-pressure conditions, due to the mechanical action of gears meshing together.
5. What are common applications for gear pumps?
Gear pumps are used in hydraulics, oil & gas, and chemical processing industries, where high-pressure fluid movement is needed.
Conclusion
In conclusion, both vane pumps and gear pumps have their distinct advantages and limitations. Vane pumps are compact, quieter, and excellent for low viscosity fluids at medium pressure, while gear pumps are versatile, durable, and capable of handling high-pressure and high viscosity environments. Understanding the differences between a vane pump and a gear pump will help you select the right one for your specific industrial needs.
For more details or assistance in choosing the best pump for your applications, feel free to contact us. Our range of products and services is designed to help you achieve optimal performance in any automation or fluid handling scenario.