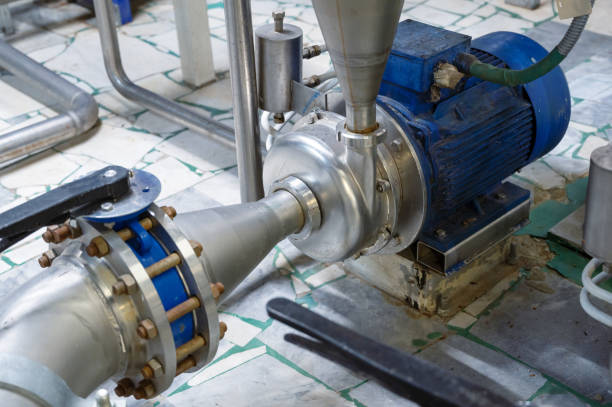
What is a Rotary Vane Pump and How Does It Work?
A rotary vane pump is a type of positive displacement pump widely used in various industrial applications, particularly in the automation industry. This pump relies on a system of sliding vanes mounted on a rotor to move fluids efficiently from the inlet to the outlet. Its capability to provide consistent flow makes it an essential component for numerous automated systems that need reliable performance. In this article, we will explore the working mechanism, components, and practical applications of rotary vane pumps in detail.
Basic Working Mechanism of Rotary Vane Pumps
The rotary vane pump consists of a rotor positioned eccentrically within a larger circular casing, also known as the chamber. The rotor contains several vanes that move freely within slots. When the rotor spins, centrifugal force pushes the vanes out, causing them to maintain tight contact with the inner walls of the chamber. This contact creates a series of sealed compartments that capture, transport, and discharge the fluid.
Fluid Intake: As the rotor turns, the volume between the vanes expands, creating a vacuum that draws fluid into the chamber from the inlet.
Compression: The rotating action continues to compress the fluid as it moves around the chamber.
Fluid Discharge: The volume decreases as the vanes approach the outlet, forcing the fluid out at a higher pressure.
The consistent movement and contact between the vanes and the chamber wall make the rotary vane pump a positive displacement pump, ensuring that each rotation of the rotor moves a fixed amount of fluid.
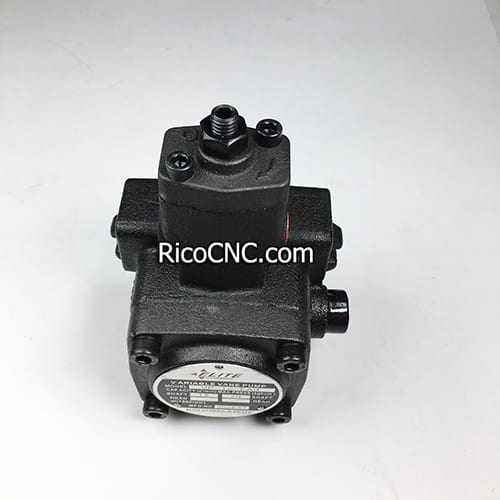
For more detailed specifications, check out our VP-12-FA3 Elite Low-Pressure Variable Vane Pump.
Components of a Rotary Vane Pump
The rotary vane pump comprises several key components, each playing an important role in its functioning:
Rotor: Central to the pump, it contains the slots in which the vanes slide.
Vanes: These are usually made of durable material like carbon or metal. They move within the slots of the rotor to maintain contact with the chamber walls.
Casing: The chamber that houses the rotor and the vanes, creating the working environment for fluid movement.
Inlet and Outlet Ports: These are the points where the fluid enters and exits the pump.
The interaction between these components ensures that the fluid is moved from one point to another, providing a consistent flow suitable for low to medium-pressure systems.
Types of Rotary Vane Pumps
Rotary vane pumps come in different variations, each tailored for specific applications:
Fixed Displacement Vane Pumps: These pumps have a fixed rotor and vane configuration, meaning the displacement (volume of fluid moved per rotation) is constant. They are suitable for applications that require a steady flow rate.
Variable Displacement Vane Pumps: Unlike fixed pumps, variable displacement vane pumps allow for adjustments in the volume of fluid being moved. This adaptability makes them suitable for applications with changing flow requirements.
Sliding Vane Pumps: These pumps use sliding vanes that adapt to the shape of the casing, making them efficient for handling low viscosity fluids like fuels and oils.
For applications where fluid characteristics or flow requirements change, you might want to explore our range of variable displacement vane pumps for added flexibility.
Advantages of Rotary Vane Pumps
Rotary vane pumps have several advantages that make them popular in various industries, including automation, manufacturing, and HVAC systems:
Consistent Flow: The positive displacement mechanism ensures a consistent and predictable flow rate.
Compact Design: They are relatively compact, making them suitable for systems where space is limited.
Versatility: These pumps can handle a wide range of fluids, including oils, fuels, and refrigerants, making them versatile for different industrial needs.
Real-World Application Example
Consider an HVAC system where refrigerant needs to be circulated consistently. A rotary vane pump is perfect for this scenario because it ensures consistent pressure without sudden surges, maintaining system stability and efficiency.
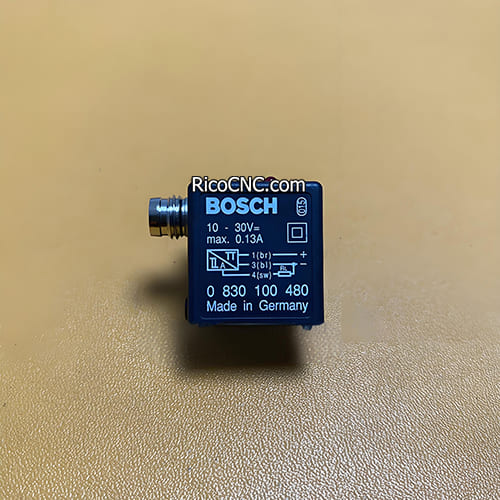
You can also use proximity sensors to monitor the functioning of these pumps. For example, our AVENTICS Proximity Sensor can provide real-time data on the pump’s operational status.
Disadvantages of Rotary Vane Pumps
Despite their benefits, rotary vane pumps have some limitations, especially when used outside of their recommended operational parameters:
Not Suitable for High Viscosity Fluids: The efficiency of these pumps reduces significantly with high viscosity fluids, as the vanes struggle to maintain smooth movement.
Not Ideal for High Pressure: The mechanical design and materials used in rotary vane pumps are not intended for high-pressure conditions, where the risk of vane deformation or failure increases.
Maintenance Requirements: The vanes are in constant contact with the chamber wall, leading to wear over time and the need for regular maintenance.
Applications of Rotary Vane Pumps in the Automation Industry
The automation industry relies heavily on rotary vane pumps for several key applications due to their reliable flow characteristics and compact size. Below are some of the primary areas where rotary vane pumps are utilized:
Hydraulic Systems: Rotary vane pumps are commonly used in hydraulic applications where consistent pressure is crucial for controlling actuators and other components.
Lubrication Systems: Many automated machines require precise lubrication. Rotary vane pumps are ideal for delivering low viscosity oils at a steady flow rate.
Fuel Dispensing: These pumps are used in automated fuel dispensing systems to ensure precise delivery without fluctuations.
For example, consider pairing rotary vane pumps with advanced servo drives to control flow rates effectively in automated systems.
Maintenance Tips for Rotary Vane Pumps
To ensure long operational life and consistent performance, proper maintenance of rotary vane pumps is essential:
Regular Lubrication: Keeping the moving parts well-lubricated will reduce friction and wear, thus extending the life of the vanes and rotor.
Inspection for Wear: Regular inspections for wear and tear, particularly on the vanes and chamber wall, are crucial. Replacing worn vanes can prevent pump failure.
Use Clean Fluids: Ensuring that the fluids used are free of contaminants can greatly reduce mechanical wear and improve efficiency.
FAQs
1. How does a rotary vane pump handle different fluid types?
Rotary vane pumps are versatile and can handle a range of fluids, from low viscosity oils to refrigerants, but they are not ideal for highly viscous or abrasive substances.
2. Can rotary vane pumps operate at high pressures?
No, rotary vane pumps are generally not suitable for high-pressure environments. The increased pressure could lead to mechanical failures, such as vane deformation or rotor damage.
3. What makes rotary vane pumps suitable for automation?
Their consistent flow, compact design, and ability to handle a range of low viscosity fluids make rotary vane pumps highly suitable for automated processes.
4. How often should rotary vane pumps be maintained?
The maintenance schedule depends on usage, but typically, regular inspections and lubrication every 3-6 months are recommended to keep the pump in good working order.
5. Are there alternatives to rotary vane pumps for high viscosity fluids?
Yes, for high viscosity fluids, gear pumps or piston pumps are more suitable alternatives as they can handle the increased mechanical load more effectively.
Conclusion
In conclusion, the rotary vane pump is an efficient and reliable type of positive displacement pump suitable for a wide range of low to medium-pressure applications involving low viscosity fluids. While they have limitations concerning high viscosity and high-pressure conditions, their versatility, compact design, and consistent flow make them invaluable in many industrial settings, especially in automation. By understanding the operation, benefits, and maintenance needs of rotary vane pumps, you can determine the best fit for your specific application.
For more guidance on selecting the right pump or to discuss your automation needs, feel free to contact us. We offer a wide range of pumps and automation solutions to meet your specific requirements.