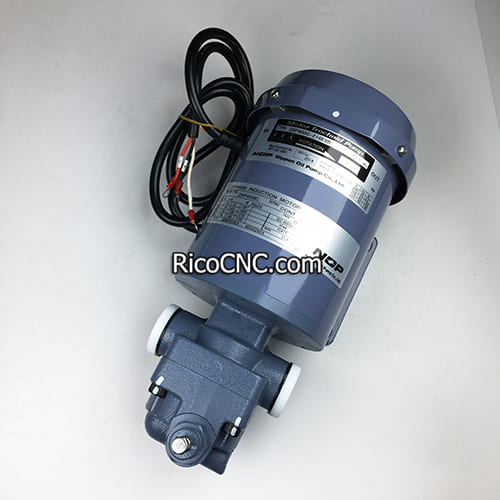
A rotary vane pump is known for its versatile use in many industries, but it is generally not recommended for applications involving high viscosity fluids or high pressures. This limitation is due to the pump's design characteristics and the physical properties of its components, which make it less efficient or even impractical for such demanding conditions. Despite this, the rotary vane pump remains a crucial element in many automation processes, especially where low to medium pressures and low-viscosity fluids are involved.
Design and Function of Rotary Vane Pumps
A rotary vane pump consists of a rotor housed within a larger circular cavity. The rotor has several vanes that slide in and out of slots to create an area that moves the fluid. When the rotor turns, centrifugal force pushes the vanes out, forming tight contact with the pump casing. The vanes, which maintain contact with the inner wall of the chamber, are responsible for moving fluid from the inlet to the outlet, thereby creating pressure.
Rotary vane pumps are classified as positive displacement pumps, meaning they displace a fixed amount of fluid for each rotation, which is crucial in achieving consistent flow. However, this design also presents specific challenges when dealing with high viscosity and high-pressure requirements.
Challenges with High Viscosity Fluids
Rotary vane pumps are not ideal for pumping high viscosity fluids for several reasons:
Increased Friction: High viscosity fluids create increased friction between the vanes and the chamber wall. This added resistance makes it harder for the vanes to move smoothly in and out of their slots, leading to potential mechanical wear and reduced efficiency.
Reduced Flow Efficiency: The movement of high viscosity fluids is more sluggish, making it difficult for the vanes to draw in and push out the fluid effectively. The pump may struggle to achieve a consistent flow, leading to reduced performance and potentially overheating.
Strain on Components: The strain on the rotor, vanes, and shaft increases significantly with high viscosity fluids. This additional strain can lead to premature failure of these components, requiring frequent maintenance and ultimately increasing operational costs.
Example: Effects of High Viscosity
Consider a pump designed to handle oil-based fluids. When the viscosity exceeds the operational limits of the pump, it causes the vanes to struggle with maintaining tight contact with the chamber wall, ultimately resulting in bypass leakage. The energy needed to maintain fluid flow increases, leading to inefficiencies and increased power consumption.
For more detailed information, check out our NOP Motor Trochoid Pumps designed to handle various viscosities with more efficient designs.
Limitations with High Pressure
The design of a rotary vane pump also limits its capability to handle high pressure applications. The reasons for this limitation are as follows:
Vane Contact and Pressure Forces: A rotary vane pump relies on the vanes making contact with the chamber wall to create a seal. At high pressures, the forces acting on the vanes become significant, potentially leading to deformation or breaking of the vanes. The increased pressure places a higher load on the rotor shaft and other internal components, making it difficult to maintain efficient performance.
Heat Generation: When the pump operates at high pressures, there is a significant increase in heat generation due to friction. This excessive heat can lead to the thermal expansion of components, causing wear and reducing the overall lifespan of the pump. Proper cooling mechanisms are necessary for high-pressure operations, which adds complexity and cost to the system.
Risk of Cavitation: At higher pressures, the chances of cavitation—the formation of vapor bubbles that implode inside the pump—also increase. Cavitation can severely damage the vanes, rotor, and pump casing, further reducing the pump’s reliability.
Suitable Alternatives for High Viscosity and High Pressure
For applications involving high viscosity or high-pressure requirements, other types of pumps are generally preferred. Here are a few suitable alternatives:
Gear Pumps: These are highly effective for high viscosity fluids due to their ability to move thick liquids consistently without losing efficiency. The gears maintain constant contact, providing a positive seal that helps achieve high pressures without significant leakage.
Piston Pumps: A piston pump is another good option for high-pressure applications. These pumps use reciprocating pistons to create high pressure and can handle both low and high viscosity fluids.
Peristaltic Pumps: Peristaltic pumps are also suitable for high viscosity fluids, as they use a rotating roller mechanism to move the fluid through a flexible hose, which reduces wear on mechanical components.
Check out our selection of servo drives that can be paired with gear pumps or piston pumps for effective performance in high-pressure systems.
Impact of Pump Type on Industrial Applications
The type of pump chosen can have a significant impact on the efficiency, cost, and maintenance requirements of an industrial system. Rotary vane pumps, although not suitable for high viscosity and high-pressure applications, have their place in many low to medium-pressure settings. Here are some scenarios where rotary vane pumps excel:
Lubrication Systems: Rotary vane pumps are ideal for pumping lubricating oils in machinery due to their consistent flow rate and low-pressure requirements.
Refrigeration and HVAC Systems: These pumps are also used to maintain consistent fluid flow in refrigeration and HVAC systems, where low viscosity refrigerants are circulated at medium pressures.
If you are dealing with varying fluid viscosities and pressure needs, consider exploring our range of variable displacement vane pumps that offer flexibility and control.
Advantages and Disadvantages of Rotary Vane Pumps
Advantages
Consistency: Rotary vane pumps provide a consistent flow rate, which is crucial in applications requiring precise control.
Versatility: These pumps are adaptable to different fluid types, including low viscosity oils, fuels, and other light fluids.
Compact Size: The compact nature of rotary vane pumps makes them suitable for systems with space constraints.
Disadvantages
Limited by Viscosity: As discussed, rotary vane pumps are not ideal for high viscosity fluids due to increased friction and reduced efficiency.
Not Suitable for High Pressures: These pumps struggle with maintaining performance under high pressure, where mechanical wear and cavitation risks increase.
Component Wear: Vanes are prone to wear and tear due to constant contact with the chamber wall, necessitating regular maintenance.
For effective pressure management in automation, we also recommend using pneumatic regulators, such as the Aventics Pneumatic Regulator, to ensure that systems remain within their operational limits.
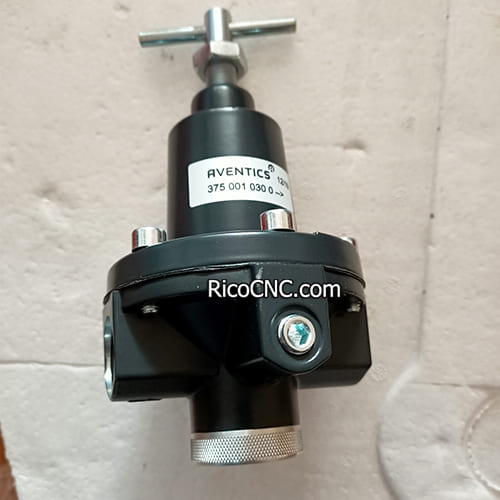
FAQs
1. Why can’t rotary vane pumps handle high viscosity fluids efficiently?
Rotary vane pumps struggle with high viscosity fluids because the increased friction causes more resistance for the vanes as they slide in and out, leading to mechanical wear and reduced efficiency.
2. What type of pump is better suited for high-pressure applications?
Gear pumps and piston pumps are generally better suited for high-pressure applications, as they have more robust designs that can handle increased pressure forces without mechanical failure.
3. Can rotary vane pumps be used for high-pressure applications if modified?
While minor modifications may help, rotary vane pumps are inherently not designed for high-pressure environments. The risk of cavitation, vane deformation, and excessive heat generation makes them unsuitable for such use.
4. How can I determine if a rotary vane pump is suitable for my application?
Consider the viscosity of your fluid and the pressure requirements of your system. If your needs fall within low to medium pressure and involve low viscosity fluids, a rotary vane pump could be ideal. Otherwise, alternative pumps may be more appropriate.
5. Are there ways to mitigate vane wear in rotary vane pumps?
Regular maintenance, lubrication, and ensuring clean fluid without contaminants can help mitigate vane wear. Using vane pumps within their recommended operational limits is also crucial.
Conclusion
In conclusion, while rotary vane pumps provide numerous advantages for low to medium-pressure applications involving low viscosity fluids, they are not suitable for high viscosity or high-pressure conditions due to increased friction, mechanical wear, and heat generation. Their design limitations make them impractical for such demanding environments. For more challenging applications, alternatives like gear pumps or piston pumps are more appropriate.
If you're considering incorporating a pump into your automation or fluid management system, feel free to contact us for expert recommendations. We offer a variety of pumps, regulators, and other components that can help you achieve optimal performance in your specific application.