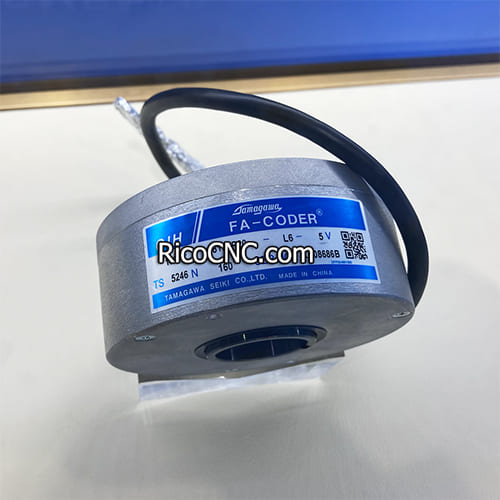
As an important measuring device, encoders are widely used in various industrial application. However, as the using time increases, encoders may have various faults. So, how to judge whether the encoder is faulty? Here are some practical judgment methods:
Methods to judge whether the encoder is faulty
1. Check the appearance: First, check whether the appearance of the encoder is damaged or deformed. If there is damage, obviously, it may not work properly.
2. Test the output signal: Test the output signal of the encoder through professional instruments. If the signal is abnormal or there is no output, it may indicate that the encoder is faulty.
3. Check the power supply and wiring: Make sure that the power supply of the encoder is normal, and the wiring terminals and wiring harness are connected correctly. If there is a problem, adjust or replace it in time.
Seven common faults of encoders
1. Signal loss: It may be caused by poor connection, loose wiring, or failure of the sensor itself. The connecting wires and connectors should be checked regularly to ensure a reliable connection.
2. Reduced resolution: Internal wear, contamination or improper use may cause the encoder resolution to decrease. The encoder should be cleaned and maintained regularly to keep it in optimal working condition.
3. Power failure: unstable power supply voltage or fault in the power supply itself can affect the normal operation of the encoder. Ensure that the power supply equipment is working properly and use voltage stabilization equipment when necessary.
4. Mechanical failure: The mechanical part of the encoder may fail due to friction, wear or improper installation. Check the status of mechanical parts regularly to ensure good lubrication and normal operation of parts.
5. Environmental interference: Environmental factors such as strong electromagnetic fields, high temperatures, and high humidity may interfere with the normal function of the encoder. Environmental factors should be considered during design, and necessary isolation and protection measures should be taken.
6. Excessive temperature: The encoder may overheat internal components and cause failures if it is in a high-temperature environment for a long time. Ensure that the encoder works within the specified temperature range and take necessary cooling measures.
7. Aging and wear: As the use time increases, the internal components of the encoder will gradually age or wear, resulting in performance degradation. Preventive maintenance should be performed regularly, and aging encoders should be replaced in time.
Seven common faults of encoders
1. Signal loss: It may be caused by poor connection, loose wiring or fault of the sensor itself. The connecting wires and connectors should be checked regularly to ensure reliable connection.
2. Reduced resolution: Internal wear, contamination or improper use may cause the encoder resolution to decrease. The encoder should be cleaned and maintained regularly to keep it in optimal working condition.
3. Power supply failure: Unstable power supply voltage or fault in the power supply itself may affect the normal operation of the encoder. The power supply equipment should be ensured to work properly and voltage stabilization equipment should be used when necessary.
4. Mechanical failure: The mechanical part of the encoder may fail due to friction, wear or improper installation. The status of mechanical parts should be checked regularly to ensure good lubrication and normal operation of parts.
5. Environmental interference: Environmental factors such as strong electromagnetic fields, high temperature and high humidity may interfere with the normal function of the encoder. Environmental factors should be considered in the design and necessary isolation and protection measures should be taken.
6. Excessive temperature: The encoder may overheat the internal components and cause failures if it is in a high temperature environment for a long time. Ensure that the encoder works within the specified temperature range and take necessary cooling measures.
7. Aging and wear: As the use time increases, the internal components of the encoder will gradually age or wear, resulting in performance degradation. Preventive maintenance should be performed regularly and aging encoders should be replaced in a timely manner.3. Causes and solutions for encoder code skipping
Encoder code skipping refers to the phenomenon that the encoder is discontinuous or jumps when outputting signals, which may be caused by the following reasons:
1. Unstable installation: The encoder is not fixed properly or there is mechanical stress during installation, causing it to move during operation. It should be reinstalled and ensured to be stable and reliable.
2. Shaft eccentricity or large mechanical transmission gap: This may cause the encoder to shake or jump during rotation. The mechanical connection should be checked and necessary adjustments or parts should be replaced.
3. Environmental vibration: There is a large vibration in the environment where the encoder is located, which affects its normal operation. Consider adding a shock absorber to reduce the impact of vibration.
For the problem of encoder code skipping, the following solutions can be taken:
1. Ensure that the encoder and mounting bracket are firm and reliable to avoid stress during installation.
2. Check whether there is gap or looseness in the mechanical connection, and replace the sleeve or coupling if necessary.
3. When used in a high-vibration environment, add a shock absorber to reduce the impact of vibration on the encoder.
In summary, understanding the common faults and causes of encoders helps to detect problems in a timely manner and take appropriate maintenance measures, which can extend the service life of the encoder and improve the overall performance and stability of the equipment.
RicoCNC can offer a wide range of Tamagawa, Elco, Kwangwoo, HEIDENHAIN etc. if you need them, please feel free contact us.