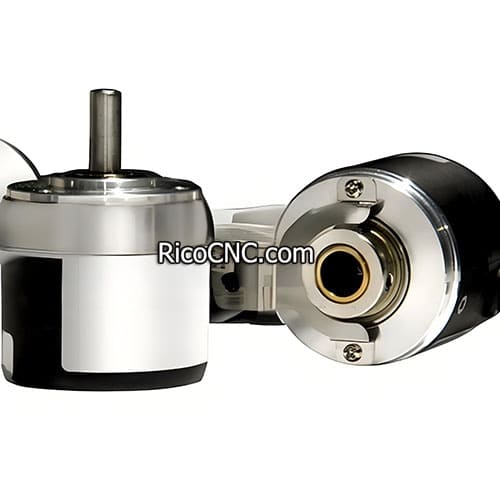
Essential Guide to Encoder Repair and Troubleshooting: Mastering Common Issues and Solutions
Are you struggling with encoder problems in your CNC automation systems? This comprehensive guide will walk you through the essential steps of encoder repair and troubleshooting, helping you maintain optimal performance and minimize downtime. Whether you're a seasoned technician or new to the field, this article will provide valuable insights into identifying, diagnosing, and resolving common encoder issues. Read on to discover expert tips, best practices, and practical solutions that will enhance your encoder maintenance skills.
What are encoders and why are they crucial in CNC automation?
Encoders are vital components in CNC automation systems, providing precise positional feedback for accurate motion control. These devices convert mechanical motion into electrical signals, enabling machines to track position, speed, and direction. Rotary encoders are particularly common in CNC applications, offering high-resolution feedback for precise movements.
Understanding the importance of encoders is crucial for maintaining the efficiency and accuracy of your CNC systems. When encoders fail or malfunction, it can lead to positioning errors, reduced productivity, and potential damage to machinery or workpieces.
What are the most common encoder issues in CNC systems?
Signal degradation
Mechanical misalignment
Contamination and environmental factors
Wiring and connection problems
Power supply issues
Identifying these common problems is the first step in effective encoder troubleshooting. By recognizing the signs of encoder failure, you can take proactive measures to prevent costly downtime and maintain optimal system performance.
How can you diagnose encoder problems using an oscilloscope?
An oscilloscope is an invaluable tool for diagnosing encoder issues. Here's how to use it effectively:
Connect the oscilloscope probes to the encoder output signals
Set the oscilloscope to display the encoder's output waveform
Analyze the waveform for irregularities, such as:
Inconsistent amplitude
Irregular pulse spacing
Noise or distortion in the signal
By examining the encoder's output waveform, you can identify issues like signal degradation, improper phasing, or electrical interference. This information is crucial for determining the root cause of encoder problems and implementing appropriate solutions.
What role does a multimeter play in encoder troubleshooting?
A multimeter is another essential tool for encoder repair and troubleshooting. Here's how it can help:
Continuity testing: Check for breaks in encoder wiring or connections
Voltage measurements: Verify proper power supply to the encoder
Resistance testing: Identify potential short circuits or open circuits
Using a multimeter in conjunction with an oscilloscope provides a comprehensive approach to encoder diagnostics, allowing you to pinpoint both electrical and mechanical issues quickly and accurately.
How can you troubleshoot encoder wiring and connection problems?
Wiring and connection issues are common causes of encoder malfunction. Follow these steps to troubleshoot:
Inspect all cable connections for loose or damaged pins
Check for proper grounding and shielding of encoder cables
Verify that cable lengths meet manufacturer specifications
Look for signs of cable damage, such as kinks or abrasions
Ensure proper termination of unused encoder wires
Proper wiring and connections are crucial for maintaining signal integrity and preventing electrical interference. Regular inspection and maintenance of encoder cables can prevent many common issues before they occur.
What are the key steps in the encoder repair process?
When an encoder requires repair, follow these key steps:
Safely remove the encoder from the machine
Disassemble the encoder, taking care to document the process
Inspect internal components for wear, damage, or contamination
Clean and lubricate mechanical parts as needed
Replace damaged components with manufacturer-approved parts
Reassemble the encoder, ensuring proper alignment and sealing
Test the repaired encoder before reinstallation
It's important to note that some encoder repairs may require specialized tools or expertise. In such cases, consider consulting with a professional repair service to ensure proper restoration of your encoder.
How can you optimize encoder output and signal quality?
Optimizing encoder output and signal quality is essential for maintaining system accuracy. Consider these tips:
Use proper shielding and grounding techniques to minimize electrical noise
Implement signal conditioning circuits to improve signal quality
Adjust encoder resolution to match application requirements
Verify proper encoder mounting and coupling to minimize mechanical errors
Regularly calibrate and align encoders to maintain accuracy
By focusing on these aspects, you can significantly improve the performance and reliability of your encoder systems.
What are the best practices for preventive maintenance of encoders?
Implementing a robust preventive maintenance program can extend the life of your encoders and reduce the likelihood of unexpected failures. Consider the following best practices:
Regularly clean and inspect encoders for signs of wear or contamination
Monitor encoder performance metrics, such as signal quality and duty cycle
Implement proper environmental controls to protect encoders from dust, moisture, and temperature extremes
Periodically check and tighten mechanical couplings and mountings
Keep detailed maintenance records to track encoder performance over time
By following these preventive maintenance practices, you can identify potential issues before they lead to system failures and extend the operational life of your encoders.
How do encoders and resolvers compare in CNC applications?
While both encoders and resolvers provide positional feedback in CNC systems, they have distinct characteristics:
Feature | Encoders | Resolvers |
---|---|---|
Output Signal | Digital or Analog | Analog |
Resolution | Generally Higher | Lower |
Durability | Moderate | High |
Cost | Varies | Generally Lower |
Environmental Resistance | Moderate | High |
Understanding the differences between encoders and resolvers can help you choose the most appropriate feedback device for your specific CNC application.
When should you consider professional encoder repair services?
While many encoder issues can be resolved in-house, there are situations where professional repair services may be necessary:
When dealing with highly specialized or proprietary encoder designs
If you lack the necessary tools or expertise for complex repairs
When time is critical, and you need a quick turnaround
For encoders that require recalibration after repair
When dealing with encoders under warranty
Professional repair services can offer expertise, specialized equipment, and access to original manufacturer parts, ensuring that your encoders are restored to optimal performance.
Key Takeaways for Effective Encoder Repair and Troubleshooting
Regularly inspect and maintain encoders to prevent common issues
Use oscilloscopes and multimeters for comprehensive diagnostics
Pay close attention to wiring, connections, and signal quality
Follow proper repair procedures and consider professional services when needed
Implement preventive maintenance practices to extend encoder life
Understand the differences between encoders and resolvers for optimal selection
Keep detailed maintenance records to track encoder performance over time
RicoCNC can supply:
TS2651N181E78 Brushless Resolvers Smartsyn Encoder Brt Smartsyn Rotary Resolver
HES-1024-2MHT 800-050-00E NEMICON Incremental Rotary Encoder Small Hollow Shaft Encoders
ERN1120 1024 ID669522-02 Heidenhain Sumtak Incremental Rotary Encoder
ERN1130 600 ID682086-03 HEIDENHAIN SUMTAK Rotary Encoder Incremental Encoder
HEIDENHAIN Encoder ERN1130 1024 ID:682086-02 ERN 1130 Series External Rotary Incremental Encoders
Welcome your inquiry.