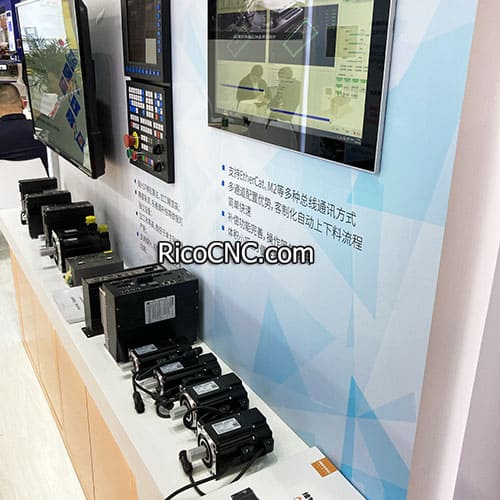
What is the difference between a 2-phase and a 3-phase AC servo driver?
In the world of industrial automation and precision motion control, AC servo drivers play a crucial role in powering and controlling servo motors. Two common types of AC servo drivers are 2-phase and 3-phase systems. Understanding the differences between these two configurations is essential for engineers, technicians, and anyone involved in designing or maintaining servo-driven systems. Let's dive deep into the distinctions between 2-phase and 3-phase AC servo drivers, exploring their characteristics, advantages, and applications.
Understanding AC Servo Drivers
Before we delve into the specifics of 2-phase and 3-phase systems, it's important to understand what an AC servo driver is and how it functions. An AC servo driver is an electronic device that controls the position, speed, and torque of an AC servo motor. It takes input commands from a controller and converts them into precise electrical signals that drive the motor. Servo drivers are essential components in many industrial applications, including CNC machines, robotics, and automation systems.
The Basics of 2-Phase AC Servo Drivers
2-phase AC servo drivers, also known as two-phase AC servo drivers, are designed to work with motors that have two sets of windings. These windings are typically arranged 90 degrees apart, creating a simple yet effective system for controlling motor rotation.
Key Characteristics of 2-Phase Systems:
Simplicity: 2-phase systems are generally simpler in design and operation compared to their 3-phase counterparts.
Lower power capacity: They are typically used for lower power applications, usually up to a few kilowatts.
Control method: 2-phase systems often use a method called "split-phase" control, where one phase is used as the main power phase, and the other is used for control.
Wiring: These systems typically require fewer wires, making installation and maintenance somewhat simpler.
Advantages of 2-Phase AC Servo Drivers:
Cost-effective: For lower power applications, 2-phase systems can be more economical.
Compact size: The simpler design often results in a smaller footprint.
Easier to implement: The control algorithms for 2-phase systems are generally less complex.
The Intricacies of 3-Phase AC Servo Drivers
3-phase AC servo drivers, as the name suggests, work with motors that have three sets of windings, typically arranged 120 degrees apart. This configuration offers several advantages over 2-phase systems, particularly in higher power applications.
Key Characteristics of 3-Phase Systems:
Higher power capacity: 3-phase systems can handle much higher power levels, making them suitable for industrial-grade applications.
Improved efficiency: The balanced nature of 3-phase power results in more efficient operation.
Smoother operation: The three phases provide more consistent torque output, reducing vibration and noise.
Advanced control methods: 3-phase systems often employ sophisticated control techniques like field-oriented control (FOC) for precise motor management.
Advantages of 3-Phase AC Servo Drivers:
Higher performance: 3-phase systems generally offer better speed control and torque characteristics.
Scalability: They can be easily scaled up for high-power applications.
Better power distribution: The balanced nature of 3-phase power leads to more efficient use of electrical resources.
MR-J3-70A Mitsubishi AC Servo Amplifier - An example of a high-performance 3-phase AC servo driver
Comparing Power and Efficiency
One of the most significant differences between 2-phase and 3-phase AC servo drivers lies in their power handling capabilities and overall efficiency.
Power Handling:
2-Phase Systems: Typically limited to applications requiring up to a few kilowatts of power.
3-Phase Systems: Can handle power ranges from a few watts to hundreds of kilowatts, making them suitable for a wide range of industrial applications.
Efficiency:
2-Phase Systems: While efficient for smaller applications, they may experience more power losses in higher power scenarios.
3-Phase Systems: Generally more efficient, especially at higher power levels, due to the balanced nature of the three-phase power distribution.
"In high-power industrial applications, 3-phase AC servo drivers are often the preferred choice due to their superior efficiency and power handling capabilities."
Control Methods and Complexity
The control methods used in 2-phase and 3-phase AC servo drivers differ significantly, impacting their performance and application suitability.
2-Phase Control:
Often uses simpler control algorithms
May employ split-phase techniques
Suitable for applications where precise position control is needed, but extreme accuracy is not critical
3-Phase Control:
Utilizes more advanced control methods like Field-Oriented Control (FOC)
Offers better torque control and dynamic response
Provides smoother operation and higher precision
Servo drives for 3-phase systems often incorporate more sophisticated control electronics and software, allowing for finer tuning and better performance in demanding applications.
Application Scenarios
The choice between 2-phase and 3-phase AC servo drivers often depends on the specific requirements of the application.
Typical 2-Phase Applications:
Small CNC machines
Light-duty robotics
Precision positioning systems in low-power scenarios
Some types of medical equipment
Common 3-Phase Applications:
Large industrial robots
High-power CNC machining centers
Conveyor systems in manufacturing
Heavy-duty automation equipment
Installation and Wiring Considerations
The installation process and wiring requirements differ between 2-phase and 3-phase systems, which can impact the overall system design and implementation.
2-Phase Wiring:
Typically requires 4 wires (2 for each phase)
Simpler wiring scheme, which can be advantageous in space-constrained applications
May require additional components for power factor correction in some cases
3-Phase Wiring:
Usually requires 4 wires (3 phases plus a neutral or ground)
More complex wiring, but offers better power distribution
Often includes built-in power factor correction
"When designing a system, consider not just the performance requirements, but also the installation complexity and space constraints when choosing between 2-phase and 3-phase servo drivers."
Cost Considerations
The cost difference between 2-phase and 3-phase AC servo drivers can be significant, especially when considering the entire system implementation.
2-Phase Cost Factors:
Generally lower initial cost for the driver unit
Simpler wiring and installation may reduce overall system cost
May require additional components for power factor correction or performance enhancement
3-Phase Cost Factors:
Higher initial cost for the driver unit
More complex installation may increase overall system cost
Better efficiency can lead to lower operating costs over time
It's important to consider both the upfront costs and the long-term operational expenses when making a decision.
Maintenance and Reliability
Maintenance requirements and overall reliability can differ between 2-phase and 3-phase AC servo drivers.
2-Phase Maintenance:
Simpler systems may require less specialized knowledge for maintenance
Fewer components can mean fewer potential points of failure
May require more frequent maintenance in high-use scenarios
3-Phase Maintenance:
More complex systems may require specialized knowledge for maintenance and troubleshooting
Higher build quality in industrial-grade systems can lead to better long-term reliability
Advanced diagnostic features in many 3-phase drivers can simplify maintenance procedures
Future Trends and Innovations
As technology continues to advance, both 2-phase and 3-phase AC servo drivers are seeing improvements in performance, efficiency, and functionality.
Emerging Trends:
Integration of IoT capabilities for remote monitoring and control
Advanced algorithms for predictive maintenance
Improved energy efficiency through better power electronics
Enhanced compatibility with renewable energy sources
Servo motors and their drivers are evolving to meet the demands of Industry 4.0 and smart manufacturing initiatives.
Making the Right Choice
Selecting between a 2-phase and a 3-phase AC servo driver requires careful consideration of various factors:
Power requirements: Assess the power needs of your application.
Precision and performance: Determine the level of accuracy and dynamic response required.
Installation constraints: Consider space limitations and wiring complexity.
Cost considerations: Evaluate both initial and long-term operational costs.
Maintenance capabilities: Assess your team's ability to maintain and troubleshoot the system.
Future scalability: Consider potential future expansion or power needs.
By carefully weighing these factors, you can make an informed decision that best suits your specific application needs.
FAQs
What are the main advantages of using a 3-phase AC servo driver over a 2-phase system?3-phase AC servo drivers offer several advantages over 2-phase systems, including higher power capacity, improved efficiency, smoother operation, and more advanced control methods. They are better suited for high-power industrial applications and provide more consistent torque output, reducing vibration and noise.How do I determine whether a 2-phase or 3-phase AC servo driver is best for my application?To determine the best choice, consider factors such as power requirements, precision needs, installation constraints, cost considerations, maintenance capabilities, and future scalability. 2-phase systems are often suitable for lower power, simpler applications, while 3-phase systems excel in high-power, high-precision industrial scenarios.