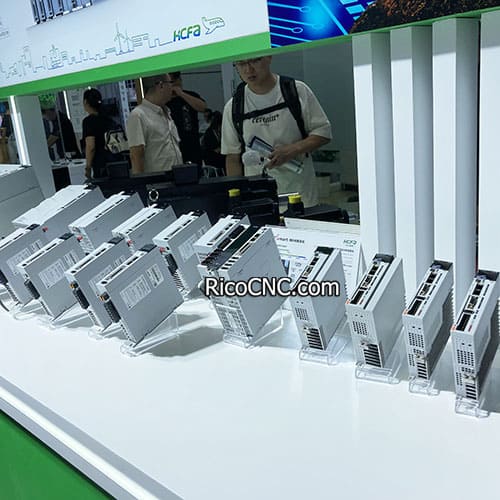
Why Choose Servo Drives Over Inverters for Servo Motors?
When it comes to motor control in automation, the choice between servo drives and inverters can be crucial. This article dives deep into why servo drives are the go-to choice for servo motors, while inverters are typically used for other types of motors. We'll explore the key differences, advantages, and applications of each, helping you make informed decisions for your automation projects. Whether you're a seasoned engineer or new to the field, this guide will shed light on the intricacies of motor control technology.
What Are Servo Motors and How Do They Differ from Other Motors?
Servo motors are a special breed in the world of electric motors. Unlike their counterparts, servo motors are designed for precision and accuracy. They're the athletes of the motor world, capable of quick starts, stops, and direction changes.Servo motors come in various types, including AC servo motors and brushless DC motors. What sets them apart is their ability to provide precise control over position, speed, and torque. This is achieved through a closed-loop control system that uses feedback from an encoder to constantly adjust the motor's performance.In contrast, standard AC or DC motors operate in an open-loop system, without the same level of feedback and precision. This fundamental difference is why servo motors require specialized servo drives for optimal performance.
What Exactly is a Servo Drive and How Does it Work?
A servo drive, also known as a servo amplifier, is the brain behind a servo motor's impressive performance. It's a sophisticated electronic device that controls the position, speed, and torque of a servo motor with high precision.Here's how a servo drive works:
It receives command signals from a control system (like a PLC or motion controller).
It interprets these signals and sends the appropriate voltage and current to the servo motor.
It continuously monitors feedback from the motor's encoder.
It makes real-time adjustments to maintain the desired position, speed, or torque.
Servo drives are designed to work in perfect harmony with servo motors, creating a high-performance motion control system. For instance, the SGDV-5R4D11A Yaskawa Servo Driver is a prime example of a modern servo drive that offers exceptional control capabilities.
What is an Inverter and How Does it Differ from a Servo Drive?
An inverter, also known as a Variable Frequency Drive (VFD) or frequency converter, is a device used to control the speed of AC induction motors. While it shares some similarities with servo drives, there are key differences:
Control Method: Inverters typically use open-loop control, adjusting motor speed by varying the frequency and voltage of the power supply.
Precision: Inverters offer good speed control but lack the high-precision positioning capabilities of servo drives.
Motor Type: Inverters are primarily used with standard AC induction motors, not servo motors.
Feedback: Most inverters don't use feedback systems, although some advanced models can incorporate simple feedback for improved performance.
Inverters are excellent for applications that require variable speed control but don't need the high precision and dynamic performance of a servo system.
Why Can't We Use Inverters for Servo Motors?
While it might seem tempting to use an inverter to control a servo motor, it's not a practical solution for several reasons:
Lack of Position Control: Servo motors require precise position control, which standard inverters cannot provide.
Feedback Integration: Servo motors use sophisticated feedback systems (encoders) that inverters are not designed to interpret.
Dynamic Performance: Servo applications often require rapid acceleration, deceleration, and direction changes, which inverters struggle to manage effectively.
Torque Control: Servo drives offer superior torque control, especially at low speeds, which is crucial for many servo applications.
Using an inverter with a servo motor would be like trying to perform brain surgery with a butter knife - technically possible, but far from optimal and potentially disastrous.
What Are the Key Advantages of Servo Drives over Inverters?
Servo drives offer several significant advantages over inverters, particularly when paired with servo motors:
Precision: Servo drives provide unparalleled accuracy in position, speed, and torque control.
Dynamic Response: They offer faster acceleration and deceleration, crucial for applications requiring quick movements.
Low-Speed Performance: Servo drives maintain full torque even at very low speeds.
Energy Efficiency: By precisely controlling power output, servo drives can be more energy-efficient in certain applications.
Versatility: They can handle a wide range of motion control tasks, from simple positioning to complex multi-axis coordination.
For example, the MR-J3-200AN Mitsubishi AC Servo Amplifier showcases these advantages, offering high-precision control for demanding automation tasks.
In What Applications Are Servo Drives Preferred Over Inverters?
Servo drives shine in applications that demand high precision, quick response, and complex motion control. Some key areas include:
CNC Machines: For accurate tool positioning and movement.
Robotics: To control robotic arms and joints with precision.
Packaging Machinery: For high-speed, accurate product handling and packaging.
Printing Presses: To ensure precise paper movement and print alignment.
Semiconductor Manufacturing: For ultra-precise component placement.
Medical Equipment: In devices requiring exact positioning, like MRI machines or surgical robots.
In these applications, the superior control offered by servo drives is not just beneficial - it's often essential for proper operation.
How Do Servo Drives Contribute to Overall System Performance?
Servo drives play a crucial role in enhancing overall system performance in several ways:
Improved Accuracy: By providing precise control, servo drives help reduce errors and improve product quality in manufacturing processes.
Increased Productivity: Their ability to handle rapid acceleration and deceleration can significantly speed up production cycles.
Flexibility: Servo drives can be easily reprogrammed for different tasks, making production lines more adaptable.
Energy Efficiency: By optimizing motor operation, servo drives can reduce energy consumption in many applications.
Reduced Maintenance: The precise control can lead to less wear and tear on mechanical components, potentially reducing maintenance needs.
For instance, the MR-JE-40A Mitsubishi Servo Amplifier is designed to enhance system performance with its advanced control features and reliability.
What Are the Cost Implications of Choosing Servo Drives over Inverters?
While servo drives often come with a higher initial cost compared to inverters, it's important to consider the long-term value:
Initial Investment: Servo drives and motors are generally more expensive than inverters and standard AC motors.
Performance Benefits: The superior performance can lead to increased productivity and higher quality output, potentially offsetting the initial cost.
Energy Savings: In applications with frequent starts and stops, servo systems can be more energy-efficient, leading to long-term savings.
Maintenance Costs: While servo systems may require specialized maintenance, their precision can lead to less wear on mechanical components.
Flexibility: The adaptability of servo systems can reduce the need for equipment changes when production requirements shift.
When evaluating costs, it's crucial to consider the entire system lifecycle and performance requirements, not just the upfront price.
How to Choose Between a Servo Drive and an Inverter for Your Application?
Selecting between a servo drive and an inverter depends on several factors:
Precision Requirements: If your application needs high-precision positioning or speed control, a servo drive is likely the better choice.
Dynamic Performance: For applications requiring rapid acceleration or frequent direction changes, servo drives excel.
Load Characteristics: Servo drives handle variable loads better, while inverters are suitable for constant-torque applications.
Speed Range: If you need full torque at very low speeds, a servo drive is preferable.
Control Complexity: For simple speed control, an inverter might suffice. For complex motion control, choose a servo drive.
Budget: Consider both initial costs and long-term operational expenses.
Energy Efficiency: Evaluate the energy consumption patterns of your specific application.
Remember, there's no one-size-fits-all solution. Carefully assess your application's needs to make the right choice.
What Does the Future Hold for Servo Drive Technology?
The future of servo drive technology looks exciting, with several trends emerging:
Increased Integration: We're seeing more servo drives with built-in motion controllers and safety features.
Enhanced Connectivity: Industry 4.0 is driving the development of servo drives with advanced communication capabilities.
Improved Energy Efficiency: Manufacturers are focusing on reducing energy consumption without compromising performance.
Artificial Intelligence: AI-enhanced servo drives could offer predictive maintenance and self-optimization features.
Miniaturization: Smaller, more powerful servo drives are being developed for space-constrained applications.
As technology advances, we can expect servo drives to become even more precise, efficient, and versatile, further widening the gap with traditional inverter technology in high-performance applications.
Key Takeaways
To sum up, here are the most important points to remember about choosing servo drives over inverters for servo motors:
Servo drives offer superior precision, dynamic performance, and torque control compared to inverters.
Inverters are suitable for simple speed control of AC induction motors, while servo drives are essential for precise motion control with servo motors.
Servo drives excel in applications requiring high accuracy, quick response, and complex motion profiles.
While initially more expensive, servo drives can offer long-term value through improved performance, energy efficiency, and flexibility.
The choice between a servo drive and an inverter should be based on your specific application requirements, considering factors like precision needs, dynamic performance, and control complexity.
As technology advances, servo drives are becoming more integrated, connected, and intelligent, further enhancing their capabilities in automation systems.
RicoCNC also supply:
SGDV-5R4D11A Yaskawa Servo Driver
MKDET1505P Panasonic AC Servo Driver
MDDLN45SE Panasonic AC Servo Driver
welcome your inquiry.