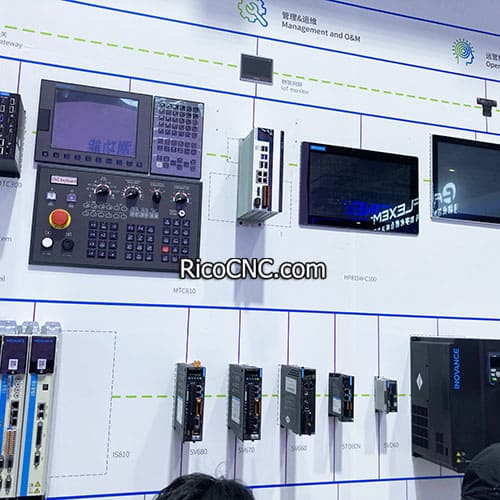
What is a servo drive, actually?
In the world of motion control and automation, servo drives play a crucial role in ensuring precise and efficient movement. But what exactly is a servo drive, and how does it function? Let's dive deep into the world of servo drives and uncover their inner workings, applications, and importance in modern industrial systems.
Understanding the Basics of Servo Drives
A servo drive is an electronic device that acts as the brain behind a servo motor system. It's responsible for controlling the position, speed, and torque of a servo motor with high precision. Think of it as the conductor of an orchestra, ensuring that every movement is perfectly timed and executed.
Servo drives are essential components in motion control systems, working in tandem with servo motors to achieve accurate and repeatable motion. They're used in a wide range of applications, from robotics and CNC machines to packaging equipment and aerospace systems.
The Anatomy of a Servo Drive
To truly understand what a servo drive is, let's break down its key components:
Power Stage: This section converts the input power into a form that can be used by the servo motor.
Control Circuit: The brain of the servo drive, responsible for processing commands and feedback signals.
Feedback Interface: Connects to the servo motor's feedback device (usually an encoder) to monitor position and speed.
Communication Interface: Allows the servo drive to receive commands from a higher-level controller or PLC.
Protection Circuits: Safeguard the drive and motor from overload, short circuits, and other potential issues.
How Servo Drives Work: The Feedback Loop
The heart of a servo drive's operation is the feedback loop. This closed-loop control system is what sets servo drives apart from other motor control methods. Here's how it works:
The servo drive receives a command signal for the desired position, speed, or torque.
It then sends the appropriate voltage and current to the servo motor.
The motor's encoder provides feedback on the actual position and speed.
The servo drive compares the actual values with the desired values.
If there's a discrepancy, the drive adjusts its output to correct the error.
This process happens continuously, thousands of times per second, resulting in extremely precise motion control.
The Importance of Proportional Gain in Servo Drives
One of the key concepts in servo drive control is proportional gain. This parameter determines how aggressively the drive responds to errors in position or speed. A higher proportional gain results in a quicker response but can lead to instability if set too high. Finding the right balance is crucial for optimal performance.
"Tuning a servo drive is like finding the sweet spot on a guitar string. Too loose, and you lose precision. Too tight, and you risk instability." - Anonymous Servo Engineer
Digital Servo Drives: The Modern Approach
While analog servo drives still exist, digital servo drives have become the standard in modern motion control systems. These drives offer several advantages:
Improved Performance: Digital processing allows for more complex control algorithms and faster response times.
Flexibility: Digital drives can be easily reprogrammed or updated to adapt to changing requirements.
Advanced Features: Functions like auto-tuning, diagnostics, and data logging are possible with digital drives.
Reduced Noise: Digital signals are less susceptible to electrical noise and interference.
Omron's R88D-GT15H-Z G-Series Servo Drive is an excellent example of a modern digital servo drive, offering high-performance motion control for various applications.
R88D-GT15H-Z Omron Servo Drive G-Series Servo Drive
Mounting and Installation Considerations
Proper installation of a servo drive is crucial for its performance and longevity. Here are some key points to consider when mounting a servo drive:
Ventilation: Ensure adequate airflow to prevent overheating.
Vibration: Mount the drive on a stable surface to minimize vibration.
EMI Protection: Shield the drive and cables from electromagnetic interference.
Accessibility: Position the drive for easy access during maintenance.
Common Applications of Servo Drives
Servo drives find applications in numerous industries due to their precision and reliability. Some common uses include:
Robotics: Controlling robotic arms and joints in manufacturing and assembly lines.
CNC Machines: Providing precise control for cutting, milling, and drilling operations.
Packaging Equipment: Ensuring accurate positioning in high-speed packaging processes.
Printing Presses: Maintaining tension and alignment in paper and textile printing.
Aerospace: Controlling flight surfaces and other critical systems in aircraft.
Choosing the Right Servo Drive
Selecting the appropriate servo drive for your application is crucial. Factors to consider include:
Power Requirements: Match the drive's power output to your servo motor's needs.
Control Modes: Ensure the drive supports the required position, velocity, or torque control modes.
Communication Protocols: Verify compatibility with your existing control systems.
Environmental Factors: Consider temperature, humidity, and vibration in the operating environment.
Safety Features: Look for drives with built-in safety functions like Safe Torque Off (STO).
Yaskawa's SGDV-5R4D11A Servo Driver is a versatile option that caters to a wide range of applications and power requirements.
SGDV-5R4D11A Yaskawa Servo Driver
Troubleshooting Servo Drive Issues
Even the best servo drives can encounter problems. Here are some common issues and their potential causes:
Motor Oscillation: Often caused by improper tuning or mechanical resonance.
Overheating: Can result from inadequate ventilation or overloading.
Position Errors: May be due to encoder issues or improper gain settings.
Noise or Vibration: Could be caused by mechanical issues or improper grounding.
The Future of Servo Drives
As technology advances, servo drives continue to evolve. Some exciting trends include:
Industry 4.0 Integration: Servo drives are becoming more connected, allowing for real-time monitoring and predictive maintenance.
Improved Energy Efficiency: New designs focus on reducing power consumption and regenerative capabilities.
Miniaturization: Smaller, more powerful drives are enabling new applications in portable and mobile devices.
Advanced Control Algorithms: Machine learning and AI are being incorporated to improve performance and adaptability.
Conclusion: The Unsung Heroes of Motion Control
Servo drives may not be the most visible components in a motion control system, but they are undoubtedly among the most critical. Their ability to provide precise, reliable, and efficient control makes them indispensable in countless applications across various industries.
As we've explored, servo drives are complex devices that combine power electronics, control theory, and advanced signal processing. Understanding their operation and capabilities is essential for anyone working in automation, robotics, or precision manufacturing.
Whether you're designing a new motion control system or looking to upgrade an existing one, choosing the right servo drive can make all the difference in achieving optimal performance and reliability.
FAQs
What's the difference between a servo drive and a VFD?
While both control electric motors, servo drives are designed for precise position, speed, and torque control using feedback systems. Variable Frequency Drives (VFDs) primarily control motor speed and are typically used with simpler induction motors.
How often should servo drives be maintained?
Regular maintenance intervals depend on the application and operating conditions. Generally, visual inspections should be performed monthly, with more thorough checks and cleanings done annually or as recommended by the manufacturer.
Can a servo drive be used with any servo motor?
Not necessarily. Servo drives and motors need to be compatible in terms of power ratings, feedback types, and control protocols. It's best to use drives and motors from the same manufacturer or verify compatibility before pairing different brands.
What causes a servo drive to fail?
Common causes of servo drive failure include overheating, voltage spikes, improper wiring, excessive vibration, and environmental factors like dust or moisture ingress. Regular maintenance and proper installation can help prevent many of these issues.
Panasonic's MKDET1505P AC Servo Driver is known for its reliability and robust design, making it less prone to common failure modes.
MKDET1505P Panasonic AC Servo Driver