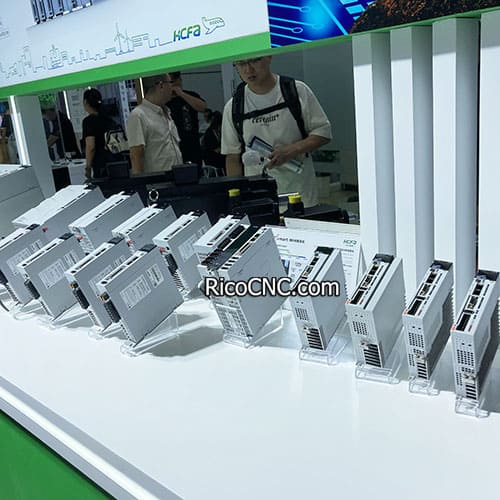
How do I choose a servo driver?
Selecting the right servo drive is crucial for optimizing your motion control system's performance. Whether you're designing a new automation setup or upgrading an existing one, choosing the appropriate servo driver can make all the difference in achieving precise, efficient, and reliable motion control. Let's dive into the key factors you need to consider when selecting a servo driver for your application.
Understanding the Basics of Servo Drives
Before we delve into the selection process, it's essential to grasp what a servo drive does. A servo drive, also known as a servo amplifier, is an electronic device that controls the position, speed, and torque of a servo motor. It works in tandem with the motor, encoder, and controller to create a closed-loop feedback system, ensuring precise motion control.
Assessing Your Application Requirements
The first step in choosing a servo driver is to thoroughly evaluate your application's needs. Consider the following aspects:
Load characteristics: Determine the inertia, friction, and external forces acting on your system.
Motion profile: Analyze the required speed, acceleration, and positioning accuracy.
Operating environment: Consider factors like temperature, humidity, and vibration.
Control requirements: Decide on the type of control (position, velocity, or torque) and the level of precision needed.
Matching Servo Drive Power to Motor Requirements
One of the most critical factors in selecting a servo driver is ensuring it can provide sufficient power to your servo motor. Consider these key parameters:
Continuous torque: The torque the motor can sustain indefinitely without overheating.
Peak torque: The maximum torque the motor can produce for short durations.
Speed range: The operational speed range of your motor.
Voltage and current ratings: Ensure the drive's output matches your motor's requirements.
"Choosing a servo drive is like finding the perfect dance partner for your motor. They need to be in sync and complement each other's strengths." - Anonymous Automation Engineer
Evaluating Drive Control Features
Modern servo drives offer a variety of control features. Consider which ones are essential for your application:
Position, velocity, and torque control modes
Tuning algorithms (auto-tuning, adaptive control)
Filtering options (notch filters, low-pass filters)
Motion profiling capabilities
Safety features (Safe Torque Off, Safe Limited Speed)
Communication Protocols and Connectivity
Ensure the servo drive you choose can communicate effectively with your existing control system. Common protocols include:
EtherCAT
PROFINET
Modbus
CANopen
Analog and digital I/O
Sizing the Servo Drive
Proper sizing of the servo drive is crucial for optimal performance and longevity. Here's a simple guide to help you size your servo drive:
Calculate the required continuous and peak current for your application.
Determine the voltage requirements of your motor.
Factor in any additional loads or inefficiencies in your system.
Choose a drive with ratings that exceed your calculated requirements by 20-30% for headroom.
Considering Environmental Factors
The operating environment can significantly impact the performance and lifespan of your servo drive. Consider these factors:
Temperature range: Ensure the drive can operate within your environment's temperature limits.
Humidity and dust: Look for drives with appropriate IP ratings if operating in harsh conditions.
Electromagnetic compatibility (EMC): Choose drives with proper shielding and filtering if EMI is a concern.
Altitude: Some drives may require derating at higher altitudes.
Evaluating Manufacturer Support and Reliability
When choosing a servo drive, consider the manufacturer's reputation and support offerings:
Technical support: Look for manufacturers offering comprehensive documentation and responsive support.
Warranty and service: Consider the warranty terms and availability of repair services.
Product lifecycle: Ensure the drive has a long expected lifespan and that spare parts will be available.
Analyzing Cost vs. Performance
While it's tempting to focus solely on the initial cost, consider the total cost of ownership:
Energy efficiency: More efficient drives can lead to significant energy savings over time.
Maintenance requirements: Some drives may require less frequent maintenance or calibration.
Downtime costs: Higher quality drives may offer improved reliability, reducing costly downtime.
Case Study: Selecting a Servo Drive for a Packaging Machine
Let's look at a practical example of selecting a servo drive for a packaging machine:
Application requirements:
Continuous torque: 2.5 Nm
Peak torque: 7.5 Nm
Maximum speed: 3000 RPM
Position control with high accuracy
EtherCAT communication
Based on these requirements, the R88D-GT15H-Z Omron Servo Drive could be an excellent choice. It offers:
Sufficient power output for the required torque
High-speed operation capability
Precise position control
EtherCAT compatibility
R88D-GT15H-Z Omron Servo Drive G-Series Servo Drive
Exploring Advanced Features
As technology evolves, servo drives are incorporating more advanced features. Consider if any of these could benefit your application:
Predictive maintenance: Drives that can monitor their own health and predict potential failures.
Energy regeneration: Capability to feed energy back into the power supply during deceleration.
Advanced tuning algorithms: Self-tuning capabilities that adapt to changing load conditions.
Integrated safety functions: Features like Safe Torque Off (STO) built directly into the drive.
The Importance of System Integration
Remember that the servo drive is just one part of your motion control system. Consider how it will integrate with other components:
Controller compatibility: Ensure the drive works seamlessly with your chosen motion controller.
Feedback devices: Check compatibility with your preferred encoder or resolver.
Power supply: Verify that your power supply can meet the drive's input requirements.
Mechanical components: Consider how the drive's characteristics will affect your mechanical design (e.g., gearing ratios, inertia matching).
Future-Proofing Your Selection
When selecting a servo drive, it's wise to think about future needs:
Scalability: Choose a drive series that offers a range of power options for future expansion.
Firmware upgrades: Look for drives that allow easy firmware updates to add new features.
Industry 4.0 readiness: Consider drives with built-in IoT capabilities for future smart factory integration.
Making the Final Decision
After considering all these factors, you should have a shortlist of suitable servo drives. To make your final decision:
Request datasheets and application notes from manufacturers.
Perform simulations if possible to verify performance.
Consult with application engineers from the manufacturer for expert advice.
Consider testing a sample drive in your actual application before full implementation.
Conclusion: Empowering Your Motion Control System
Choosing the right servo driver is a critical step in creating an efficient and reliable motion control system. By carefully considering your application requirements, matching drive specifications to your motor needs, and evaluating additional features and support, you can select a servo drive that will enhance your system's performance and longevity.
Remember, the perfect servo drive is one that not only meets your current needs but also provides room for future growth and adaptation. Whether you're working on a packaging machine, a robotic arm, or a CNC system, the right servo drive can make all the difference in achieving precise, efficient, and reliable motion control.
As technology continues to advance, servo drives like the SGDV-5R4D11A Yaskawa Servo Driver are pushing the boundaries of what's possible in motion control. By staying informed about the latest developments and carefully evaluating your options, you can ensure that your motion control system remains at the cutting edge of performance and efficiency.
SGDV-5R4D11A Yaskawa Servo Driver
FAQs
How often should I replace my servo drive?
The lifespan of a servo drive can vary greatly depending on usage and environmental conditions. With proper maintenance, a high-quality servo drive can last 10-15 years or more. However, it's important to monitor performance and consider replacement if you notice decreased efficiency or increased errors.
Can I use a servo drive with a different brand of servo motor?
While it's generally recommended to use servo drives and motors from the same manufacturer for optimal compatibility, many drives can work with motors from different brands. However, you'll need to ensure that the drive's specifications (voltage, current, feedback type) match the motor's requirements and may need to perform additional tuning.
What's the difference between a servo drive and a VFD?
While both control electric motors, servo drives are designed for precise position, speed, and torque control using a closed-loop feedback system. Variable Frequency Drives (VFDs) primarily control motor speed and are typically used with simpler induction motors in applications that don't require the same level of precision.
How do I troubleshoot servo drive errors?
Start by checking the error code displayed on the drive or through the setup software. Common issues include wiring problems, encoder faults, or tuning issues. Consult the manufacturer's manual for specific troubleshooting steps. If the problem