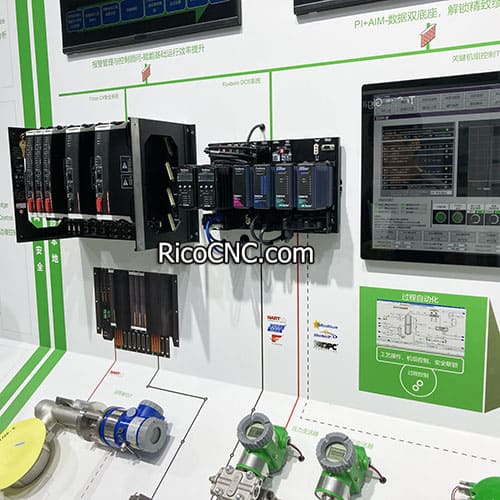
What is the difference between servo drive and normal drive?
In the world of industrial automation and motion control, understanding the distinctions between various drive systems is crucial for optimizing performance and efficiency. Two common types of drives that often come up in discussions are servo drives and normal drives (also known as variable frequency drives or VFDs). While both serve the purpose of controlling motors, they have significant differences in their design, functionality, and applications. Let's delve into the intricacies of these drive systems to uncover what sets them apart.
The Fundamentals of Servo Drives
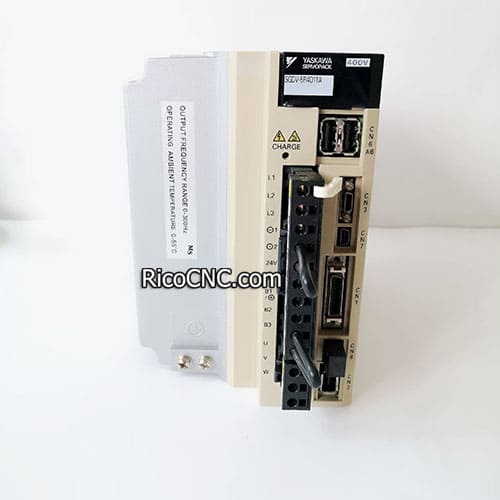
Servo drives are specialized electronic devices designed to control servo motors with precision and accuracy. These sophisticated systems are the backbone of many high-performance motion control applications. At their core, servo drives work in conjunction with servo motors to create a closed-loop control system that constantly monitors and adjusts the motor's position, speed, and torque.
Key Features of Servo Drives:
Precise Position Control: Servo drives excel in applications requiring exact positioning.
High Dynamic Response: They can quickly accelerate, decelerate, and change direction.
Feedback Mechanism: Utilizes encoders or resolvers for real-time position and speed feedback.
Torque Control: Capable of maintaining consistent torque across a wide speed range.
Complex Motion Profiles: Can execute intricate motion sequences with ease.
Servo drives are commonly found in robotics, CNC machines, packaging equipment, and other applications where precision is paramount. For instance, the SGDV-5R4D11A Yaskawa Servo Driver is a prime example of a high-performance servo drive used in industrial settings.
Understanding Normal Drives (VFDs)
Normal drives, often referred to as variable frequency drives (VFDs) or AC drives, are designed to control the speed and torque of AC induction motors. These drives operate on a different principle compared to servo drives and are typically used in applications where precise positioning is not the primary concern.
Characteristics of Normal Drives:
Speed Control: Primarily focused on controlling motor speed rather than position.
Energy Efficiency: Can significantly reduce energy consumption in variable-speed applications.
Open-Loop Operation: Generally operate without feedback, though some advanced models may incorporate it.
Soft Start Capability: Reduces mechanical stress and electrical surge during motor startup.
Simple Motion Control: Best suited for applications with straightforward speed requirements.
VFDs are commonly used in pumps, fans, conveyors, and other applications where variable speed control is needed without the necessity for high-precision positioning.
The Core Differences
Now that we've outlined the basics of both drive types, let's explore the key differences that set them apart:
1. Control Mechanism
Servo Drives: Operate in a closed-loop system with constant feedback, allowing for precise control of position, speed, and torque.
Normal Drives: Typically function in an open-loop system, focusing primarily on speed control without direct feedback.
2. Motor Type
Servo Drives: Designed to work with servo motors, which are often permanent magnet motors with built-in feedback devices.
Normal Drives: Commonly used with standard AC induction motors, which are simpler and more robust.
3. Precision and Accuracy
Servo Drives: Offer extremely high precision, often down to fractions of a degree or micron-level positioning.
Normal Drives: Provide good speed control but lack the fine positioning capabilities of servo systems.
4. Dynamic Response
Servo Drives: Exhibit rapid response times and can quickly adjust to changing load conditions.
Normal Drives: Have slower response times and are less adept at handling rapid changes in speed or load.
5. Torque Control
Servo Drives: Maintain full torque at zero speed and across a wide speed range.
Normal Drives: Typically have reduced torque at lower speeds, especially without additional feedback mechanisms.
6. Complexity and Cost
Servo Drives: Generally more complex and expensive due to their advanced control capabilities and feedback systems.
Normal Drives: Usually simpler and more cost-effective, making them suitable for less demanding applications.
Applications: Where Each Drive Shines
Understanding the strengths of each drive type helps in selecting the right solution for specific applications:
Servo Drive Applications:
Robotics and automation
CNC machining centers
Packaging machinery
Printing presses
Medical equipment
Semiconductor manufacturing
For example, the MR-JE-40A Mitsubishi Servo Amplifier is often used in precision manufacturing processes where accurate positioning is critical.
Normal Drive (VFD) Applications:
HVAC systems
Pumps and compressors
Conveyor belts
Fans and blowers
Mixers and agitators
Simple machine tools
Energy Efficiency Considerations
Both servo drives and normal drives can contribute to energy efficiency, but in different ways:
Servo Drives: Achieve energy savings through precise motion control, minimizing wasted movement and optimizing power usage during operation.
Normal Drives: Provide significant energy savings in variable-speed applications by adjusting motor speed to match the load requirements, especially in systems that traditionally used mechanical means for speed control.
Integration and Control Systems
The integration of drives into larger control systems is another area where differences become apparent:
Servo Drives: Often integrated into complex motion control systems, working in tandem with programmable logic controllers (PLCs) and motion controllers. They frequently communicate via high-speed fieldbus protocols.
Normal Drives: While they can be integrated into control systems, they are often used in simpler setups with basic start/stop and speed control functions. Many modern VFDs, however, are incorporating more advanced communication capabilities.
Maintenance and Reliability
Maintenance requirements and overall reliability can vary between the two drive types:
Servo Drives: Generally require more specialized maintenance due to their complexity. The feedback devices (encoders) may need occasional calibration or replacement.
Normal Drives: Typically have fewer components and are often more robust in harsh industrial environments. They may require less frequent maintenance but still benefit from regular check-ups.
Choosing Between Servo and Normal Drives
Selecting the right drive for your application involves considering several factors:
Precision Requirements: If your application demands high accuracy and repeatability, a servo drive is likely the better choice.
Speed Control Needs: For applications where variable speed is the primary concern, a normal drive (VFD) may suffice.
Load Characteristics: Consider the torque requirements across the speed range and whether the load varies significantly.
Dynamic Performance: Assess how quickly the system needs to respond to changes in speed or position.
Cost Considerations: Evaluate the budget against the performance requirements of your application.
Environmental Factors: Consider the operating environment and any specific protection requirements.
Conclusion
In conclusion, the choice between a servo drive and a normal drive (VFD) depends largely on the specific requirements of your application. Servo drives excel in precision motion control, making them ideal for applications that demand high accuracy, quick response times, and complex motion profiles. On the other hand, normal drives offer a cost-effective solution for applications that primarily require speed control without the need for precise positioning.
Understanding these differences is crucial for engineers and system designers to make informed decisions when selecting drive systems. By carefully considering the unique needs of each application, you can choose the drive that will provide the best performance, efficiency, and value for your specific use case.
Whether you opt for a high-precision servo drive or a versatile VFD, the key is to align the drive's capabilities with your application's requirements. As drive technology continues to evolve, staying informed about the latest advancements will help you make the best choices for your motion control needs.
FAQs
Can a normal drive (VFD) be used in place of a servo drive?
While VFDs can control motor speed effectively, they generally lack the precision positioning capabilities of servo drives. In applications requiring exact position control or complex motion profiles, a servo drive is typically necessary. However, for simpler speed control applications, a VFD may be sufficient and more cost-effective.
How do servo drives achieve such precise control?
Servo drives achieve precise control through a closed-loop feedback system. They use feedback devices like encoders to constantly monitor the motor's position and speed. This real-time information allows the drive to make rapid adjustments, ensuring the motor follows the commanded position or speed with high accuracy.
Are servo drives more energy-efficient than normal drives?
Both servo drives and normal drives can be energy-efficient, but in different ways. Servo drives are more efficient in applications requiring precise movements, as they minimize wasted motion. Normal drives (VFDs) excel in energy efficiency for variable-speed applications, particularly those that previously used mechanical means for speed control. The most energy-efficient choice depends on the specific application requirements.