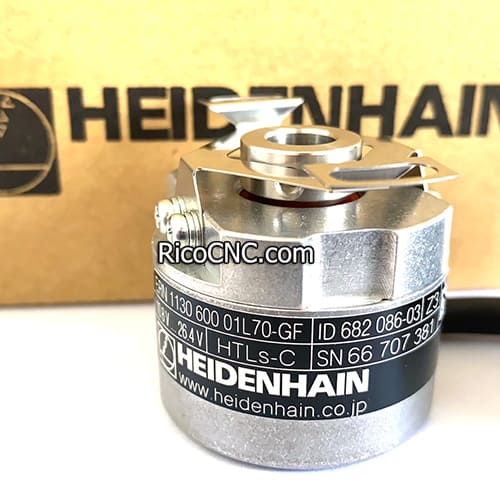
How Does a Magnetic Encoder Work?
Magnetic encoders are widely used in various industries for providing precise position and motion control information. These devices play a significant role in ensuring accurate control of motor-driven systems by translating physical movement into digital signals. This article will provide a comprehensive understanding of how a magnetic encoder works, its different types, applications, and the benefits it brings to motion control solutions.
What Is a Magnetic Encoder?
A magnetic encoder is a type of position sensor that uses magnetic fields to determine the position, speed, and direction of a moving object. It consists of a rotor with magnets and a sensor that detects changes in the magnetic field. The information gathered by the sensor is then converted into electrical signals, which are used for feedback in control systems.
Magnetic encoders come in different types, such as rotary and linear encoders, each providing unique advantages depending on the application. Rotary magnetic encoders measure angular displacement, while linear encoders measure position along a straight line.
Basic Components of a Magnetic Encoder
A magnetic encoder typically comprises:
Rotor with Magnets: The rotor is equipped with magnets, often arranged in a specific pattern to create north and south poles.
Sensing Element: A magnetic field sensor detects the changing magnetic fields produced by the rotor's movement.
Signal Processing Unit: This unit processes the signals from the sensor and converts them into digital or analog outputs that are compatible with the control system.
These components work together to create a seamless measurement system that can provide accurate feedback for motors and other types of machinery.
How Does a Magnetic Encoder Work?
The working principle of a magnetic encoder is based on the interaction between a rotating magnetic field and a sensor. The rotor, fitted with magnets, generates a magnetic field as it moves. The sensor detects variations in the magnetic flux as the rotor turns, which is then processed into an electrical signal representing the position or movement.
Steps in the Operation of a Magnetic Encoder
Magnet Rotation: When the motor shaft or other moving part rotates, it turns the rotor of the magnetic encoder, which contains embedded magnets.
Magnetic Field Sensing: The sensors, often Hall-effect or magnetoresistive sensors, detect the changes in the magnetic field.
Signal Processing: The detected magnetic fluctuations are converted into electrical signals, which can either be incremental or absolute based on the type of encoder.
Output Signal: The processed signals are sent to the control unit as digital pulses or analog signals, representing the position, speed, or direction of the rotor.
Types of Magnetic Encoders: Incremental vs. Absolute
Magnetic encoders can be categorized into incremental and absolute types, each serving different purposes and offering distinct advantages.
Incremental Magnetic Encoders
Incremental encoders provide output signals corresponding to the changes in position. The output is in the form of pulses, which can be counted to determine the relative movement of the object. Key features include:
Simplicity: They are simpler and generally more affordable.
Resolution: The resolution depends on the number of pulses generated per revolution, which can be adjusted based on the application.
Application: These encoders are used in scenarios where only relative positioning is needed, such as in motor speed control or conveyor systems.
Absolute Magnetic Encoders
Absolute magnetic encoders, in contrast, provide an exact position from the moment the system is powered on. This is achieved by assigning unique values to each position of the rotor. Features include:
Unique Positioning: Each position is assigned a specific code, allowing the encoder to provide a unique output for every point along the rotor's path.
No Re-Calibration: Absolute encoders do not require recalibration after a power cycle, making them ideal for safety-critical applications where accuracy is paramount.
Application: These encoders are commonly used in robotic arms, medical devices, and other situations requiring exact, non-relative positioning.
Magnetic Encoder Applications
Magnetic encoders are versatile and find use in numerous fields due to their reliability and robustness in harsh environments. Here are some of the common applications:
Industrial Automation: Magnetic encoders are used in robotics and automated machinery to control positioning and ensure accurate movement.
Automotive Systems: These encoders provide feedback in systems such as anti-lock brakes and power steering to enhance vehicle control.
Motor Control: Magnetic encoders are crucial in controlling servo motors and brushed DC motors, allowing precise adjustments in speed and position.
Renewable Energy: Wind turbines use magnetic encoders to accurately track rotor blade angles, ensuring optimal energy output.
Advantages of Magnetic Encoders
Resistance to Dust and Dirt: Magnetic encoders are robust and not affected by contaminants such as dust, oil, or moisture, unlike optical encoders.
Durability: The absence of mechanical contact ensures a longer lifespan and reduces the need for maintenance.
High Resolution: Advanced magnetic encoders can achieve high levels of resolution, making them suitable for applications requiring precise control.
Comparing Magnetic and Optical Encoders
Feature | Magnetic Encoders | Optical Encoders |
---|---|---|
Resistance to Environment | High (Resistant to dirt) | Low (Sensitive to dust) |
Durability | Very Durable | Can be prone to damage |
Cost | Generally more affordable | Costlier, especially at high resolutions |
Resolution | High, but generally lower compared to optical | Very High |
Applications | Harsh environments, general-purpose use | Clean environments, precision instruments |
The comparison table above illustrates the trade-offs between magnetic and optical encoders. Magnetic encoders are a better choice for rugged environments, while optical encoders excel in situations where ultra-high precision is necessary.
Internal Links for Further Information
For those seeking more information on encoder technology, you might find the following resources insightful:
Understand more about the various types of servo drives and their interaction with encoders.
Discover our products like the SGDV-5R4D11A Yaskawa Servo Driver which uses advanced encoder feedback systems.
Learn more about Mitsubishi AC Servo Amplifiers, designed for precision motor control using encoder feedback.
Frequently Asked Questions About Magnetic Encoders
How does a magnetic encoder differ from an optical encoder?
Magnetic encoders use magnetic fields to detect position, making them more durable and resistant to environmental contaminants compared to optical encoders that rely on light.
What are the benefits of using a magnetic encoder?
Magnetic encoders offer high durability, resistance to contaminants, and are generally more affordable compared to optical encoders, especially in harsh environments.
Can magnetic encoders be used for both linear and rotary applications?
Yes, magnetic encoders are available in both linear and rotary configurations, making them versatile for different types of motion control systems.
Do magnetic encoders require regular maintenance?
Magnetic encoders require minimal maintenance due to their contactless operation, unlike other types of encoders which have moving parts that can wear out over time.
Conclusion
Magnetic encoders are a versatile and reliable solution for providing position and speed feedback in various industries, from automotive to renewable energy. Their ability to withstand harsh environments, coupled with their durability and low maintenance, make them an excellent choice for many applications. By choosing the right encoder type—incremental or absolute—industries can ensure accurate control and feedback, leading to more efficient and effective operations.
If you're looking for advanced encoder solutions, our experts are here to help you navigate your options and find the best fit for your needs. Whether it's for motor control, robotics, or any other automation challenge, our comprehensive range of products will have the right fit for you.