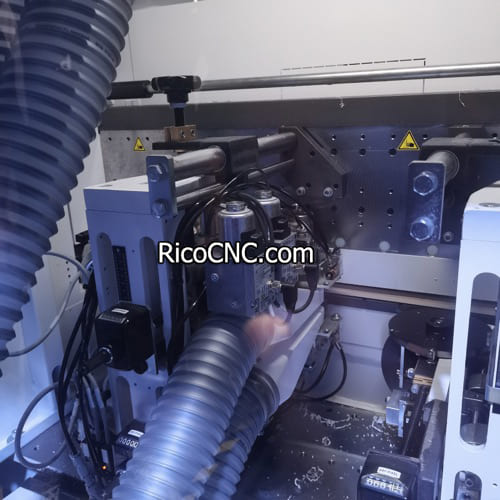
How to Check an Air Solenoid Valve
Air solenoid valves are vital components in numerous pneumatic systems. They manage the flow of air to control actuators and other pneumatic devices, making them a key part of industrial automation, automotive, and HVAC systems. However, air solenoid valves can encounter problems over time, such as blockages, electrical failures, or pressure drops, leading to operational inefficiencies. In this article, we will explore how to effectively check and troubleshoot an air solenoid valve, ensuring that it functions correctly and maintains the efficiency of your pneumatic system.
Understanding the Air Solenoid Valve
An air solenoid valve is an electrically controlled valve that uses a solenoid coil to move a plunger, thereby opening or closing different ports to manage the direction of compressed air. It often consists of several critical components:
Valve Body: The casing that holds all parts.
Solenoid Coil: Generates a magnetic field when current flows through it.
Plunger and Spring: The plunger moves due to the electromagnetic force, while the spring brings it back to its original position.
Checking the air solenoid valve involves both electrical tests and physical inspections to verify proper functionality.
Basic Working Principle
When power is applied to the solenoid coil, it generates a magnetic field that moves the plunger inside the valve body. This movement directs the airflow to different ports, enabling control over pneumatic devices. Understanding how the valve works is the first step toward diagnosing any issues it may face.
For a specific product example, check out the 4KB219-00 CKD 24VDC Pneumatic Solenoid Valve, known for its efficiency in managing airflow in automation systems.
Tools Required for Testing
Before you start testing an air solenoid valve, make sure to gather the necessary tools:
Multimeter: To check for electrical continuity and voltage.
Pressure Gauge: To measure the pressure differential across the valve.
Screwdrivers and Wrenches: To disassemble the valve if required.
Compressed Air: To blow out any obstructions.
How to Test an Air Solenoid Valve
Step 1: Check the Power Supply
The first step in diagnosing a solenoid valve issue is to check if it's receiving adequate power. Connect a multimeter to the solenoid's terminals and measure the voltage while the valve is supposed to be energized.
Voltage Requirement: Verify that the voltage matches the specified rating of the valve, usually between 12V to 240V, depending on the application.
Common Issues
No Voltage: If there is no voltage, check upstream connections, including wiring and the control circuit.
Incorrect Voltage: An incorrect voltage reading could indicate a problem with the power supply or control circuitry.
For a better understanding of solenoid valves used in automation systems, consider the R414002403 Aventics Pneumatic Solenoid Valve.
Step 2: Test the Solenoid Coil
Next, use a multimeter to test the solenoid coil for electrical continuity. This step ensures that the coil is intact and capable of generating the magnetic field necessary for valve operation.
Set the Multimeter to Ohms: Place the multimeter on the resistance (Ohms) setting.
Check Resistance: Measure the resistance across the terminals of the solenoid coil.
Expected Results:
Normal Resistance: Most solenoid coils have a resistance range of 20-100 Ohms, depending on their type and design.
No Continuity: If the multimeter shows infinite resistance, the coil is burnt out and needs replacement.
Zero Resistance: Indicates a short circuit, and the coil must also be replaced.
Step 3: Listen for the Solenoid Click
When the solenoid valve is energized, you should hear a click sound, which indicates that the plunger is moving. This sound confirms that the solenoid coil is functioning correctly, and the plunger and spring are working as they should.
No Click Sound: This could mean a faulty coil, a stuck plunger, or insufficient voltage.
Step 4: Check Air Pressure and Flow
Using a pressure gauge, check the air pressure on both sides of the valve. A difference in the expected flow rate may indicate a problem with the valve’s ability to open and close fully.
Pressure Differential: Ensure that there is a proper pressure differential as specified for the valve. Many solenoid valves require a minimum differential to operate correctly.
Step 5: Inspect for Blockages
If the solenoid valve still doesn’t function properly, it might have internal blockages. Disconnect the valve from the system and use compressed air to clear out any debris. Inspect the ports and orifices to make sure they are clean and free from obstructions.
For another high-quality solenoid valve that’s easy to maintain, take a look at the 2241.52.00.39.02 Pneumax Pneumatic Solenoid Valve.
Common Problems and Solutions
1. No Response from Valve
If there is no response when the valve is energized, possible causes include:
Faulty Coil: Test with a multimeter; replace if necessary.
No Power Supply: Verify voltage at the terminals.
Stuck Plunger: Disassemble and inspect the plunger; clean or replace as needed.
2. Valve Leaking
Leaks are often caused by worn seals or improper seating of the plunger. Regular maintenance, such as inspecting and replacing worn O-rings and seals, can help avoid leaks.
3. Slow Operation
A slow response might indicate a spring failure or blockage within the valve body. Clean the valve thoroughly, and check the spring tension to ensure it is adequate.
Tips for Maintaining Air Solenoid Valves
Routine Inspections: Regular checks for electrical continuity, pressure levels, and physical blockages can help maintain valve health.
Clean Regularly: Use compressed air to blow out any debris that may accumulate over time.
Check Electrical Connections: Ensure that all electrical connections are tight and free of corrosion.
Internal Links for Further Information
If you're interested in more details on solenoid valves and other related automation products, check out these links:
For automation system servo motors, see the MSMD042P1U Panasonic AC Servo Motor for CNC Machines.
Discover the SH31003P11A2000 Schneider Electric AC Servo Motor for reliable performance in automation.
Learn more about the SGMJV-01ADA21 YASKAWA AC Rotary Servo Motors for efficient motor control.
Frequently Asked Questions About Air Solenoid Valves
1. How do I know if my air solenoid valve coil is functioning?
To check if the coil is functioning, use a multimeter to measure the resistance across the coil terminals. If it falls within the expected range (usually 20-100 Ohms), the coil is functional.
2. Why is my air solenoid valve not clicking?
If you don't hear a click, it may indicate an issue with the coil, insufficient voltage, or a stuck plunger. Perform a multimeter test on the coil and ensure the voltage supply is correct.
3. What causes an air solenoid valve to leak?
Leaks are often caused by worn seals or improper seating of the internal components. Routine maintenance, including checking and replacing seals, can help prevent leaks.
4. Can I clean a solenoid valve without disassembling it?
While it is recommended to disassemble the valve for a thorough cleaning, you can use compressed air to blow through the ports and remove loose debris without disassembling.
Conclusion
Checking an air solenoid valve is essential for ensuring the smooth operation of your pneumatic systems. By following the steps outlined in this guide—such as testing the power supply, coil, and pressure—you can effectively diagnose and fix common issues. Regular maintenance, including cleaning and replacing worn components, will further enhance the longevity and reliability of your solenoid valve.
If you need any more information or are interested in purchasing solenoid valves, feel free to reach out. We provide a wide range of automation products tailored to your needs.