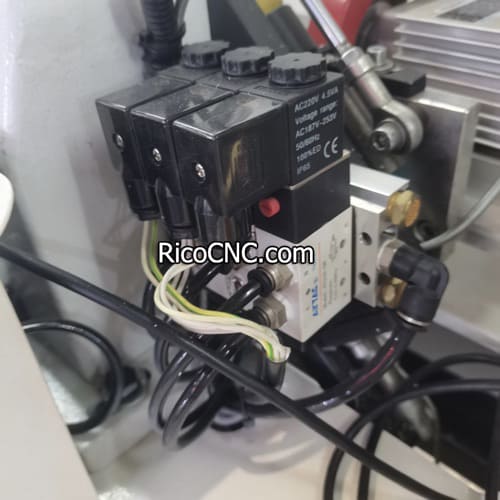
How Does a Proportional Solenoid Valve Work?
Proportional solenoid valves are vital components in modern automation, providing fine control over fluid flow and pressure. Unlike conventional on-off solenoid valves, proportional solenoid valves can regulate the output to adjust flow rates with precision, making them indispensable in applications where precision control is necessary, such as in industrial automation, HVAC systems, and automotive systems. In this article, we will explore how a proportional solenoid valve works, the underlying principles, and the components that contribute to its functionality.
What is a Proportional Solenoid Valve?
A proportional solenoid valve is a type of control valve designed to manage the flow or pressure of a fluid in a proportional manner to an input signal. Unlike conventional solenoid valves that are either fully open or fully closed, proportional solenoid valves adjust the opening incrementally, allowing for more refined control.
These valves receive input signals—commonly pulse-width modulation (PWM) or a continuous voltage/current—which regulates the movement of the valve’s internal components. As a result, the flow rate or pressure is proportionally controlled to match the requirements of the application.
Applications: Used in industrial automation, water treatment, hydraulic systems, and pneumatic systems for precise control.
Key Components: Include a solenoid coil, valve spool, and control electronics.
For more information on proportional valves in industrial settings, check out the SGMJV-01ADA21 YASKAWA AC Rotary Servo Motors, which demonstrate the type of control precision that is critical for applications involving proportional control.
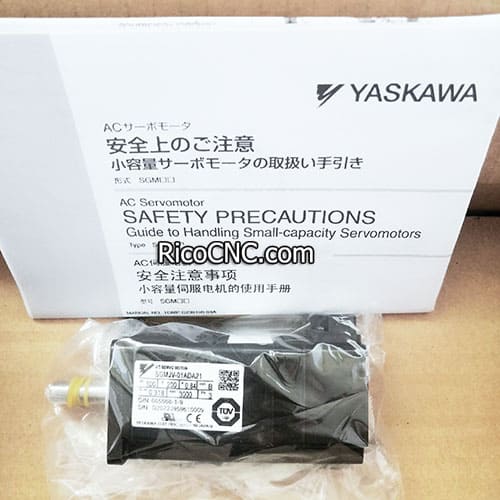
How Do Proportional Solenoid Valves Work?
1. The Role of the Solenoid Coil
The solenoid coil is at the core of how these valves work. When energized, the solenoid coil creates a magnetic field, which pulls the plunger or moves a spool inside the valve. The movement of the spool determines how much fluid can pass through the valve. The current applied to the coil controls the strength of the magnetic field and, in turn, the positioning of the valve components.
Variable Control: Unlike traditional valves, the current supplied is varied, which proportionally moves the plunger, resulting in partial opening or closing.
Input Signals: The input signal can either be a continuous current or a PWM signal, each offering different advantages for control precision.
For instance, proportional solenoid valves are often used with MSMD042P1U Panasonic AC Servo Motors for CNC Machines, which require precise flow regulation.
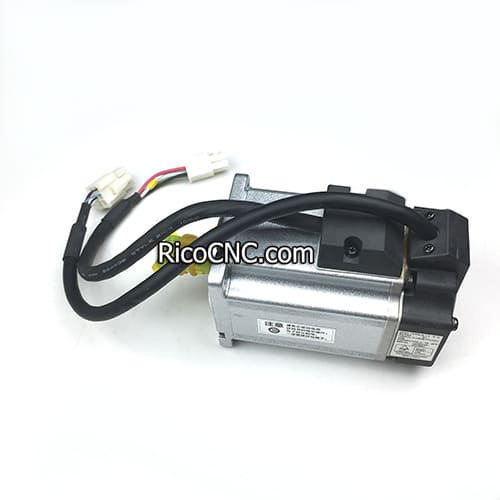
2. Pulse Width Modulation (PWM)
Pulse Width Modulation (PWM) is one of the most common techniques used to regulate the duty cycle of the valve. By adjusting the width of the pulses that energize the solenoid coil, the valve can be controlled to allow varying degrees of fluid flow.
Duty Cycle: The duty cycle refers to the percentage of time the valve is open during each pulse cycle. For instance, a 50% duty cycle means that the valve is open half the time, offering medium flow.
Advantages: PWM control provides efficient modulation and avoids the excessive heating that may occur with continuous control currents.
Using a PWM signal can significantly improve energy efficiency and accuracy in flow control applications.
3. Control Electronics and Feedback
Proportional solenoid valves often incorporate control electronics that interpret the input signal and convert it into movement. These control systems may also include feedback loops to ensure the valve’s position matches the desired flow rate or pressure.
Closed-Loop Control: Sensors monitor the actual flow or pressure, and adjustments are made automatically to achieve the desired set point.
Open-Loop Control: In some systems, a preset signal adjusts the valve position without feedback. This method is simpler but less precise.
For advanced control needs, consider exploring the SH31003P11A2000 Schneider Electric AC Servo Motor, which offers precision suitable for applications involving proportional solenoid valves.
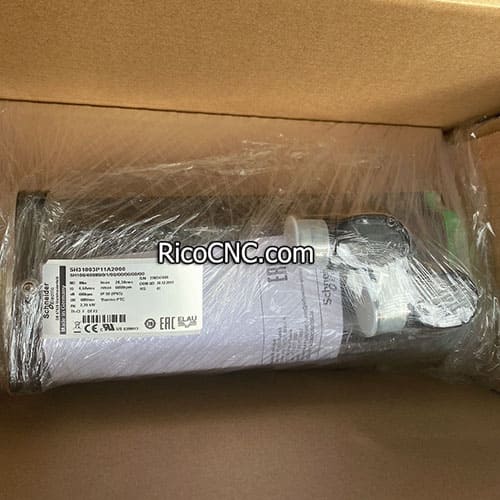
Types of Proportional Solenoid Valves
1. Direct-Acting Proportional Valves
In direct-acting proportional valves, the solenoid coil directly moves the valve spool or poppet, controlling the flow or pressure. These valves are best for applications requiring low flow rates and high precision.
Advantages: Simple construction, reliable operation.
Applications: Ideal for precise fluid control in laboratory settings or low-pressure systems.
2. Pilot-Operated Proportional Valves
Pilot-operated valves use a smaller, direct-acting valve to regulate a larger spool that handles the main flow. This design is typically used for high-pressure and high-flow applications.
Advantages: Able to control large flows with minimal effort.
Applications: Common in hydraulic systems and industrial machinery.
3. Digital Proportional Valves
These valves utilize digital control systems and can be interfaced with automation systems for high precision. They often feature digital displays and programmable settings.
Advantages: Greater accuracy, easy integration with digital control systems.
Applications: Industrial processes requiring automated control and remote operation.
Advantages of Proportional Solenoid Valves
1. Precise Flow and Pressure Control
The primary advantage of proportional solenoid valves is the ability to precisely regulate flow and pressure. Unlike on/off valves, they can be adjusted to provide any value between fully open and fully closed.
Flexible Adjustment: The ability to make incremental adjustments ensures that the system operates at its optimal performance level.
Stable Operation: Provides a more stable system as sudden changes in pressure and flow can be avoided.
2. Energy Efficiency
These valves are more energy-efficient compared to traditional solenoid valves, particularly when PWM control is used. By varying the duty cycle, the valve only consumes power as needed, avoiding waste.
Lower Heat Generation: Since PWM avoids continuous current, less heat is generated in the solenoid coil, increasing its longevity.
3. Compact Design
Proportional valves are designed to be compact yet powerful. They can fit into small spaces while still providing the control needed for complex automation tasks.
Space-Saving: Ideal for applications where space is limited but control performance is crucial.
How to Select a Proportional Solenoid Valve
When choosing a proportional solenoid valve, consider the following factors to ensure that it meets the system’s requirements:
Flow Rate: Determine the maximum flow rate required for your application.
Pressure Requirements: Select a valve that can handle the system’s pressure range without degradation.
Signal Type: Choose whether a PWM or continuous current control signal best suits your needs.
Material Compatibility: Ensure the valve body and seals are compatible with the working fluid—common materials include stainless steel and brass.
For high-quality options, explore the R911312640 MSK030C-0900-NN-M1-UP1-NSNN Bosch Rexroth Serie MSK Motor, which offers precision control and reliability for integrated automation solutions.
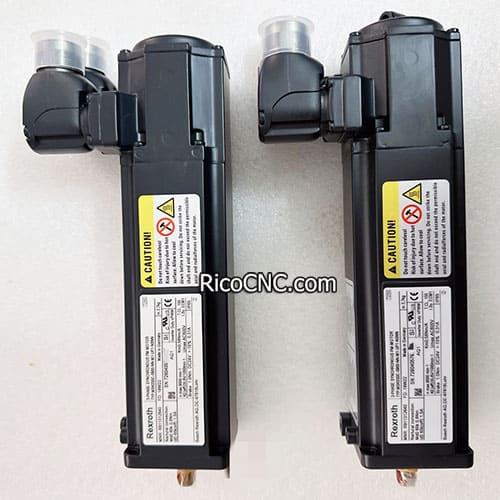
Applications of Proportional Solenoid Valves
1. Hydraulic Systems
In hydraulic systems, proportional solenoid valves are used to precisely control fluid flow, providing accurate pressure adjustments and preventing system overload.
Example: Hydraulic presses and construction equipment benefit from proportional valves for controlled lifting and lowering.
2. HVAC Systems
Heating, ventilation, and air conditioning (HVAC) systems rely on proportional valves for controlling airflow and refrigerant flow. These valves ensure comfortable climate control by accurately adjusting flow rates.
Advantage: Minimizes energy consumption while maintaining desired temperatures.
3. Industrial Automation
In industrial automation, proportional valves are used to manage fluid flows in processes such as chemical dosing, mixing, and spraying.
Automation: Integrates seamlessly with other control systems for synchronized automation.
Frequently Asked Questions About Proportional Solenoid Valves
1. What is the main advantage of a proportional solenoid valve over a standard solenoid valve?
The main advantage is the precise control of fluid flow or pressure. Unlike standard valves that are either fully open or closed, proportional valves allow for incremental adjustments, enabling more fine-tuned operations.
2. How does PWM improve the efficiency of a proportional solenoid valve?
PWM helps in controlling the valve with minimal energy loss by modulating the duty cycle. This means that power is used only when needed, reducing overall consumption and preventing overheating.
3. Can proportional solenoid valves be used for both gas and liquid applications?
Yes, they can be used for both gas and liquid applications as long as the materials of the valve are compatible with the specific fluid in use.
4. Are proportional solenoid valves suitable for high-pressure applications?
Pilot-operated proportional valves are specifically designed to handle high-pressure applications, making them suitable for industrial machinery and hydraulic systems.
Conclusion
Proportional solenoid valves play a significant role in various industries by providing the ability to finely control fluid flow and pressure. Whether through direct action, pilot operation, or digital control, these valves offer significant advantages in terms of precision, efficiency, and system stability. Choosing the right proportional solenoid valve depends on factors such as flow rate, pressure range, and control signal requirements. Regular maintenance and correct installation further enhance the reliability and lifespan of these essential automation components.
If you need further assistance in selecting the right proportional solenoid valve for your application, feel free to contact us. We are here to help you achieve precise and reliable control in all your automation projects.