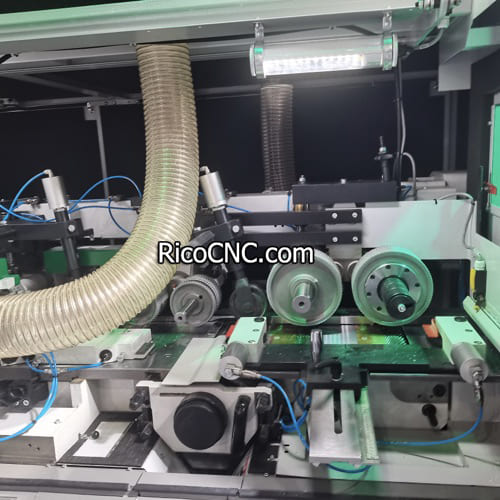
How to Check if a Solenoid Valve is Bad
Solenoid valves are an integral part of many systems, including sprinkler systems, irrigation networks, and industrial automation. They serve the purpose of controlling the water flow, air, or other fluids by using electrical signals to open or close a valve. Over time, solenoid valves can experience wear and tear, leading to potential malfunctions. Identifying and troubleshooting a bad solenoid valve is crucial for keeping systems operational and efficient. This guide will take you through the process of how to check if a solenoid valve is bad, with practical methods and insightful tips for maintenance and troubleshooting.
Understanding the Solenoid Valve
A solenoid valve is an electrically operated valve used to control the flow of fluid or gas within a system. It consists of a solenoid coil, a plunger, and a valve body with inlet and outlet ports. The coil generates a magnetic field when energized, which moves the plunger to either open or close the valve.
Solenoid valves are found in numerous applications including:
Sprinkler Systems: Used to control water pressure and flow.
- Irrigation Systems: To regulate the flow of water to plants.
- HVAC and Industrial Systems: Used for controlling air or gases.
Understanding how these components work is the first step to diagnosing any problems that may occur.
Tools Needed to Test a Solenoid Valve
Before testing a solenoid valve, make sure to gather these essential tools:
Multimeter: To test for continuity and voltage.
- Screwdrivers and Wrenches: To disassemble the valve if necessary.
- Pressure Gauge: To check pressure drop across the valve.
- Power Supply: To energize the solenoid coil.
Signs That a Solenoid Valve is Bad
There are several signs that a solenoid valve may be faulty or failing:
No Response: When power is applied, there is no audible click or mechanical movement in the valve.
- Valve Stuck Open or Closed: The valve remains in one state despite input from the control system.
- Leaks: Leaking from the valve body or port connections.
- Electrical Issues: The solenoid coil may be burnt out, resulting in no magnetic field formation.
For practical solutions and products, refer to the 4KB219-00 CKD 24VDC Pneumatic Solenoid Valve, which is known for reliable performance in automation systems.
Step-by-Step Guide to Testing a Solenoid Valve
Step 1: Check Power Supply
The first step in testing a solenoid valve is to verify that it is receiving the proper power supply. Using a multimeter, check the voltage at the solenoid terminals while the valve is energized.
Voltage Requirement: Ensure the voltage matches the valve's rating, usually between 12V to 240V, depending on the application.
- No Voltage: If there is no voltage, the issue may be upstream—inspect the wiring and control circuit.
Step 2: Test the Coil for Continuity
To check the solenoid coil for continuity, set your multimeter to the resistance (Ohms) setting and measure the resistance across the two terminals of the coil.
Expected Values:
Normal Resistance: Most solenoid coils have a resistance range between 20-100 Ohms. A reading within this range indicates that the coil is functioning correctly.
- No Continuity (Infinite Resistance): This means the coil is open and must be replaced.
- Zero Resistance: This could mean the coil is short-circuited, requiring replacement.
Step 3: Listen for the Solenoid Click
When the valve is powered, you should hear a click that indicates the plunger is moving inside the valve. This sound confirms that the coil is generating a magnetic field strong enough to move the plunger.
No Click: If you don't hear a click, this could mean that the coil is damaged, or the plunger is stuck.
Step 4: Test for Pressure and Flow
Check the pressure across the solenoid valve with a pressure gauge. A significant pressure drop could indicate a restriction or blockage within the valve.
Normal Operation: During normal valve operation, there should be a minimal pressure drop across the valve if it is fully open.
- Restricted Flow: A high pressure drop could indicate a partially closed valve or an obstruction.
For reference on efficient solenoid valves used in regulating air pressure, check out the R414002403 Aventics Pneumatic Solenoid Valve.
Step 5: Visual Inspection
Perform a visual inspection of the valve to look for any signs of damage or wear.
Check Seals: The seals on the valve should be intact without any visible damage.
- Inspect Ports: Look for any blockages in the ports that may be restricting flow.
- Check Plunger: Disassemble the valve to check if the plunger moves freely. The spring should bring it back to its original position when de-energized.
Step 6: Test Solenoid Response Time
The response time of a solenoid valve is another indicator of its health. If the valve takes longer to activate or deactivate, it may indicate a failing spring or a weakened solenoid coil.
Quick Response: In a properly functioning valve, the solenoid should activate and deactivate almost immediately after the power is applied or removed.
For an example of a reliable solenoid valve with quick response, consider the 2241.52.00.39.02 Pneumax Pneumatic Solenoid Valve.
Common Problems and Solutions
1. Coil Burnout
Problem: If the solenoid coil is burnt out, the magnetic field will not form.
Solution: Test the coil with a multimeter. Replace if resistance is not within the expected range.
2. Valve Stuck
Problem: The plunger inside the valve might become stuck due to dirt or other blockages.
Solution: Disassemble the valve and clean all the internal components. Make sure the plunger moves freely.
3. No Voltage
Problem: There is no voltage reaching the solenoid coil.
Solution: Verify the power supply and check the control circuit for any loose connections or blown fuses.
Tips for Maintaining Solenoid Valves
Regular Cleaning: Clean the valve body and ports regularly to prevent debris from causing blockages.
- Routine Checks: Regularly test the solenoid coil and plunger for proper movement.
- Electrical Connections: Ensure all electrical connections are secure and free from corrosion.
Frequently Asked Questions About Solenoid Valves
1. How do I know if my solenoid valve is working properly?
Check for a clicking sound when power is applied. You can also use a multimeter to verify the coil resistance, which should fall within the specified range.
2. Can I clean a solenoid valve without disassembling it?
Yes, you can use compressed air to blow through the ports to remove any loose debris. However, disassembly is recommended for thorough cleaning.
3. What could cause a solenoid valve to leak?
Leaks may be caused by worn seals or improper seating of the plunger. Routine maintenance, including inspecting and replacing seals, can prevent leaks.
4. Why does my solenoid valve make a buzzing sound?
A buzzing sound usually indicates that the voltage supplied to the solenoid coil is not stable, or the coil is failing. Ensure you are using the correct voltage for the valve.
Conclusion
Solenoid valves are key components in many automation and control systems. By following the steps outlined in this guide—such as checking the power supply, testing the solenoid coil, and inspecting for mechanical blockages—you can easily diagnose and address issues with a solenoid valve. Regular maintenance, such as cleaning and replacing worn parts, will help prolong the life of your solenoid valve and ensure it operates smoothly.
If you need further assistance or wish to explore a wide range of solenoid valves and other automation components, feel free to contact us. We are committed to providing solutions tailored to your specific requirements.