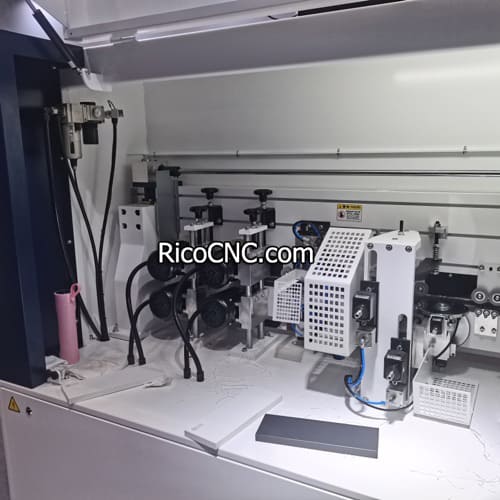
What Causes a Limit Switch to Go Bad?
Limit switches are crucial components in many mechanical and industrial systems, often serving as safety interlocks or position detectors. Their reliable function ensures the smooth operation of processes ranging from household furnaces to sophisticated industrial automation systems. Despite their importance, limit switches can sometimes fail, leading to operational issues or system malfunctions. In this article, we will explore the primary causes of limit switch failures, helping you to understand how to prevent and address these issues effectively.
Common Causes of Limit Switch Failure
1. Mechanical Wear and Tear
One of the most common reasons a limit switch goes bad is mechanical wear and tear. Limit switches often involve physical contact, such as a lever or actuator coming into direct contact with another part. Over time, this constant contact leads to wear, which can reduce the precision or efficiency of the switch. Components like the lever arm or actuator may become worn down, and the switch might no longer operate correctly.
For instance, in a furnace, a limit switch is frequently used to detect airflow or regulate temperature. Repeated use can eventually cause the components to become loose or ineffective, leading to failure. Worn contacts can lead to arcing, which causes damage that compromises the switch's reliability.
Related Product Insight
If you're experiencing frequent wear issues, consider upgrading to a high-durability solenoid valve such as the 5728400620 AVENTICS Single Solenoid Valve. This component offers enhanced durability under tough conditions.
2. Exposure to High Temperatures
Another leading cause of limit switch failure is exposure to high temperatures. Many limit switches are used in environments where temperature control is critical—such as in furnaces or industrial heaters. Prolonged exposure to excessive heat can deteriorate the internal components of the switch, including the springs, plastic insulators, and electrical contacts.
For example, in a furnace limit switch, the high limit switch plays a key role in ensuring that the furnace does not exceed safe operating temperatures. However, if exposed to temperatures higher than it’s rated for, the internal components can become damaged, resulting in malfunction or complete failure. It is essential to ensure that the limit switch is appropriate for the temperature range in which it will be operating to prevent such damage.
3. Accumulation of Dirt and Debris
The accumulation of dirt, dust, and other debris can also cause a limit switch to fail. In industrial settings or dusty environments, these elements can infiltrate the switch mechanism, making it difficult for the internal components to move freely. This is especially true for mechanical limit switches, which have moving parts that are particularly vulnerable to dirt buildup.
For instance, blower motors that rely on limit switches for detecting movement can suffer malfunctions if dirt clogs the switch mechanism. Preventive maintenance such as regularly cleaning and checking the switches can help reduce the risk of failure due to dirt and dust.
4. Electrical Arcing and Contact Damage
Electrical arcing occurs when the current flow between two contacts jumps a gap, which can lead to the erosion or burning of these contacts. This kind of arcing is particularly common in high-load systems, where limit switches are used to control powerful machinery or electrical systems. Over time, arcing can damage the contacts within the switch, rendering it unreliable or entirely non-functional.
When the contacts become burned or pitted, the limit switch may start failing to open or close properly, ultimately leading to operational issues. This is why many high-duty applications use contactors or relays in combination with limit switches to manage the current load more effectively.
Related Product Insight
To manage electrical load effectively and reduce arcing issues, consider using the 4WE6Y62/EG24N9K4 R900561276 Bosch Rexroth Directional Spool Valve. This valve can work well in tandem with limit switches to manage high electrical loads efficiently.
5. Improper Installation or Alignment
Incorrect installation or improper alignment of the limit switch can also lead to failure. If the switch is not installed in the right position or the actuator isn’t correctly aligned, the switch may not activate properly. This can lead to situations where the system believes the limit has not been reached, causing overheating or improper movement of mechanical parts.
For example, in a conveyor belt system, a limit switch is used to detect the position of objects. If the switch is poorly aligned, it might miss the target position, leading to unplanned stoppages or potentially damaging the product or machinery. To avoid such problems, it's essential to carefully follow installation guidelines and test the switch’s response to ensure proper alignment.
6. Vibration and Shock
Vibration and mechanical shock are common in many industrial settings, particularly those involving heavy machinery or equipment that operates continuously. Limit switches, especially those with moving mechanical parts, are sensitive to such vibrations and can suffer from mechanical fatigue as a result. Constant vibration can loosen internal components or even cause wiring to disconnect, leading to operational inconsistencies or failure.
For machinery subject to high levels of vibration, consider using non-contact limit switches or proximity sensors, which tend to be more robust against physical disturbances. Non-contact switches use magnetic or optical sensors, which are not as susceptible to mechanical shock as traditional mechanical limit switches.
7. Overloading the Limit Switch
Many limit switches are designed with specific current ratings. Exceeding these ratings—known as overloading—can cause overheating of the electrical contacts, leading to damage or burnout. Each switch is designed to handle a particular load, and applying excessive current can not only damage the switch itself but also create a risk for other connected components.
It is crucial to understand the load ratings of the limit switch being used and ensure it matches the application requirements. In cases where there are higher current demands, integrating relays or contactors alongside limit switches is often a recommended practice.
Related Product Insight
The 0820060126 Bosch Rexroth Pneumatic Directional Valve is designed to work effectively in automation systems, especially when paired with limit switches for load control.
Preventive Measures to Avoid Limit Switch Failures
To minimize the risk of limit switch failure, several preventive measures can be employed:
Regular Maintenance: Clean and inspect limit switches periodically to prevent issues due to dust and debris accumulation.
- Use Appropriate Components: Choose limit switches that are rated for the specific environmental conditions, such as temperature and current load.
- Proper Installation: Ensure that the switch is installed according to manufacturer guidelines, with proper alignment to avoid any operational issues.
- Load Management: Use relays or contactors to prevent overloading limit switches.
Monitor Environmental Conditions: Ensure that limit switches are placed in environments where they are protected from vibration, shock, and extreme temperatures.
Frequently Asked Questions
1. What causes a limit switch to wear out?
The most common reasons are mechanical wear from continuous physical contact, accumulation of debris, and arcing of electrical contacts over time. Regular maintenance and proper installation can help prevent early wear.
2. How do high temperatures affect a limit switch?
High temperatures can damage the internal components of a limit switch, such as springs, plastic parts, and contacts, causing the switch to malfunction or fail completely. It is essential to use switches rated for the expected temperature range.
3. Can I repair a faulty limit switch?
In some cases, you may be able to repair a faulty limit switch by cleaning contacts or replacing worn parts. However, in most situations, it is recommended to replace the switch to ensure reliable performance.
4. How can I avoid overloading a limit switch?
To avoid overloading, ensure that the current flowing through the switch does not exceed its rated capacity. For higher loads, use relays or contactors alongside limit switches.
Conclusion
Understanding the causes of limit switch failures is key to ensuring reliable and consistent operation in both residential and industrial settings. Whether it's due to mechanical wear, environmental factors, or overloading, identifying and mitigating these causes can save time, money, and prevent downtime. Regular maintenance, proper installation, and careful component selection can go a long way in extending the life of your limit switches.
If you're looking to optimize your automation systems and require the right components to keep things running smoothly, explore our range of limit switches and other industrial automation products. Contact us today to learn more about how we can support your automation needs.