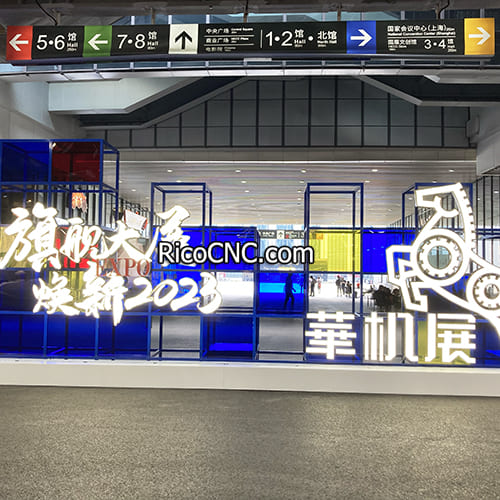
In which applications gear pumps are used?
Gear pumps are versatile and efficient fluid transfer devices that find applications across a wide range of industries. These pumps are known for their simple design, reliability, and ability to handle various fluids. In this comprehensive guide, we’ll explore the diverse applications of gear pumps and why they are the preferred choice in many sectors.
Understanding Gear Pump Basics
Before diving into specific applications, let’s briefly review how gear pumps work. Gear pumps use two or more intermeshing gears to create fluid flow. As the gears rotate, they create a seal between the gear teeth and the pump casing, trapping and moving fluid from the inlet to the outlet.
There are two main types of gear pumps:
External Gear Pumps: These have two gears that mesh together inside a casing.
Internal Gear Pumps: These have one external gear that rotates inside an internal gear.
Both types operate on the same principle of creating cavities that trap and move fluid, resulting in a smooth, pulse-free flow that’s proportional to the rotational speed of the gears.
Learn more about TOP-212HWMVD NOP Oil pump Trochoid pump
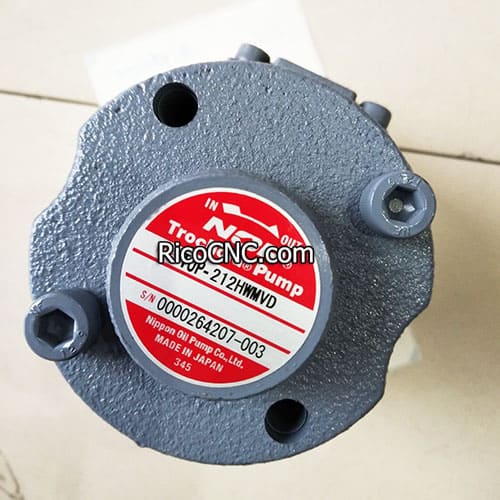
Automotive Industry Applications
Gear pumps play a crucial role in various automotive systems:
Engine Lubrication: External gear pumps are commonly used for engine oil circulation, ensuring proper lubrication of moving parts.
Fuel Transfer: In fuel systems, gear pumps help move fuel from the tank to the engine.
Power Steering: Some power steering systems use gear pumps to pressurize hydraulic fluid.
Transmission Fluid Circulation: Gear pumps help circulate and pressurize transmission fluid in automatic transmissions.
The reliability and consistent flow of gear pumps make them ideal for these critical automotive applications.
Industrial Manufacturing Processes
In the manufacturing sector, gear pumps are indispensable for various processes:
Polymer Processing: Gear pumps are used in extrusion and injection molding machines to precisely meter and pressurize molten polymers.
Paint and Coatings: The smooth, pulse-free flow of gear pumps is perfect for applying paints and coatings evenly.
Adhesive Application: In woodworking and packaging industries, gear pumps accurately dispense adhesives.
Chemical Processing: Gear pumps handle a wide range of chemicals, making them suitable for various chemical manufacturing processes.
Oil and Gas Industry Applications
The oil and gas sector relies heavily on gear pumps for several applications:
Refinery Operations: Gear pumps transfer various petroleum products within refineries.
Lubrication Systems: In large machinery used in oil extraction, gear pumps ensure proper lubrication.
Fuel Transfer: From storage tanks to distribution points, gear pumps help move different types of fuels.
Offshore Platforms: Gear pumps are used in various systems on offshore oil rigs, including hydraulic power units.
Food and Beverage Industry
Gear pumps find numerous applications in food processing:
Dairy Processing
Beverage Production
Confectionery
Edible Oils
The ability of gear pumps to handle viscous fluids makes them particularly useful in these applications.
Pharmaceutical and Cosmetic Industries
In these industries, precision and cleanliness are paramount:
Drug Manufacturing: Gear pumps accurately meter and mix liquid medications.
Agricultural Applications
Gear pumps play a vital role in modern agriculture:
Irrigation Systems: Pumping water and liquid fertilizers in precision agriculture.
Pesticide Application: Accurately dispensing pesticides and herbicides.
Marine Industry Uses
On ships and in marine environments, gear pumps are used for:
Hydraulic Systems: Powering various hydraulic equipment on ships, such as cranes and winches.
Lubrication Systems: Ensuring proper lubrication of marine engines and other machinery.
Discover R900932111 PGF3-31/040RE07VE4 Bosch Rexroth Gear Pump Hydraulic Internal Gear Pump
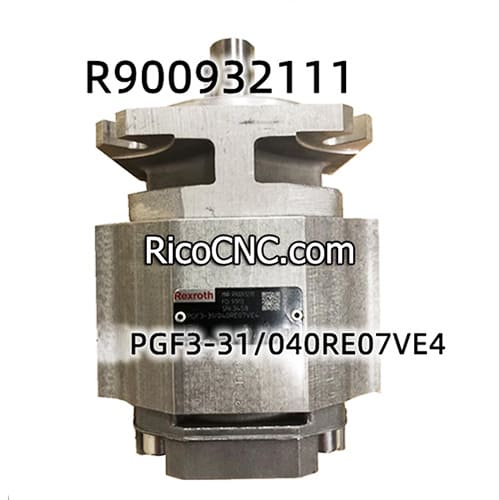
Construction and Mining Equipment
Heavy machinery in these industries often relies on gear pumps:
Hydraulic Systems: Powering various hydraulic components in excavators, bulldozers, and other heavy equipment.
Lubrication Systems: Ensuring proper lubrication of large machinery used in mining and construction.
Aerospace Applications
In the aerospace industry, gear pumps are used in several critical systems:
Fuel Systems: Transferring fuel within aircraft fuel systems.
Hydraulic Systems: Powering various hydraulic components in aircraft, including landing gear and control surfaces.
Renewable Energy Sector
As the world shifts towards renewable energy, gear pumps find new applications:
Wind Turbines: Used in hydraulic systems for blade pitch control and yaw systems.
Solar Thermal Plants: Circulating heat transfer fluids in concentrated solar power systems.
Wastewater Treatment
In water and wastewater treatment plants, gear pumps are used for:
Chemical Dosing: Precisely adding treatment chemicals to water.
Sludge Transfer: Moving thick sludges and slurries within treatment processes.
Pulp and Paper Industry
The pulp and paper industry relies on gear pumps for various processes:
Pulp Transfer: Moving pulp slurries between different stages of paper production.
Chemical Addition: Adding various chemicals used in paper manufacturing.
Textile Industry Applications
In textile manufacturing, gear pumps are used for:
Dye Application: Precisely metering and applying dyes to fabrics.
Sizing Application: Applying sizing agents to yarns and fabrics.
HVAC Systems
Heating, Ventilation, and Air Conditioning systems use gear pumps for:
Refrigerant Circulation: In large industrial refrigeration systems.
Chilled Water Systems: Circulating chilled water in commercial and industrial cooling systems.
Heating Systems: Circulating hot water or oil in heating systems.
Geothermal Heat Pumps: Moving heat transfer fluids in geothermal HVAC systems.
Explore ELITE VP Series VP30-FA3DH Variable Displacement Vane Pump
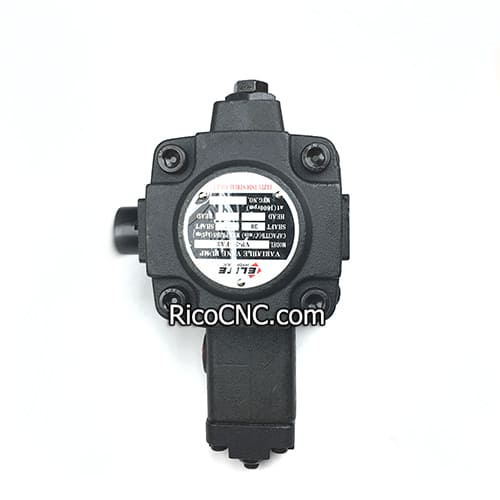
Frequently Asked Questions
What makes gear pumps suitable for handling viscous fluids?
Gear pumps excel at handling viscous fluids due to their positive displacement design. The close tolerances between the gears and the pump casing create a strong seal, allowing them to move thick liquids efficiently. This makes them ideal for applications involving oils, syrups, and other high-viscosity fluids.
Can gear pumps handle abrasive materials?
While gear pumps can handle mildly abrasive materials, prolonged use with highly abrasive fluids can cause wear on the gears and casing. For moderately abrasive applications, hardened materials or special coatings can be used to extend the pump’s life. However, for highly abrasive materials, other pump types might be more suitable.
How do gear pumps compare to other pump types in terms of efficiency?
Gear pumps are known for their high efficiency, especially when handling medium to high-viscosity fluids. They typically have efficiencies ranging from 75% to 90%, depending on the specific design and operating conditions. This high efficiency, combined with their ability to maintain consistent flow rates, makes them a preferred choice in many industrial applications.
Are gear pumps self-priming?
Most gear pumps are not inherently self-priming. However, they can become self-priming once the pump casing is filled with fluid. Some gear pump designs incorporate features to improve their self-priming capabilities, such as air bleed valves or specialized priming chambers.
How do you maintain a gear pump to ensure long-term reliability?
To maintain a gear pump:
Regularly check and change the lubricating fluid as recommended by the manufacturer.
Inspect seals and replace them when worn to prevent leaks.
Monitor the pump for unusual noises or vibrations, which could indicate wear or misalignment.
Ensure the pump is operating within its designed pressure and flow range.
Clean the pump thoroughly when changing fluids to prevent contamination.
Follow the manufacturer’s recommended maintenance schedule for inspections and part replacements.
Conclusion
Gear pumps are truly versatile workhorses in the world of fluid handling. Their applications span across numerous industries, from automotive and manufacturing to food processing and renewable energy. The key advantages of gear pumps – their simple design, reliability, and ability to handle a wide range of fluids – make them an indispensable component in many industrial processes.
As we’ve explored, gear pumps play crucial roles in engine lubrication, chemical processing, food production, and even in cutting-edge renewable energy technologies. Their ability to provide smooth, pulse-free flow and handle viscous fluids with high efficiency sets them apart in many applications.
For engineers, plant managers, and anyone involved in fluid handling systems, understanding the capabilities and applications of gear pumps is crucial. Whether you’re designing a new process, upgrading existing equipment, or troubleshooting a system, considering gear pumps as a solution could lead to improved efficiency and reliability in your operations.
The wide-ranging applications of gear pumps demonstrate their importance in keeping industries running smoothly. From the food on our tables to the fuel in our vehicles, gear pumps play a hidden but vital role in many aspects of our daily lives. As we continue to innovate and develop new technologies, it’s clear that gear pumps will remain a fundamental component in the machinery of industry and technology.