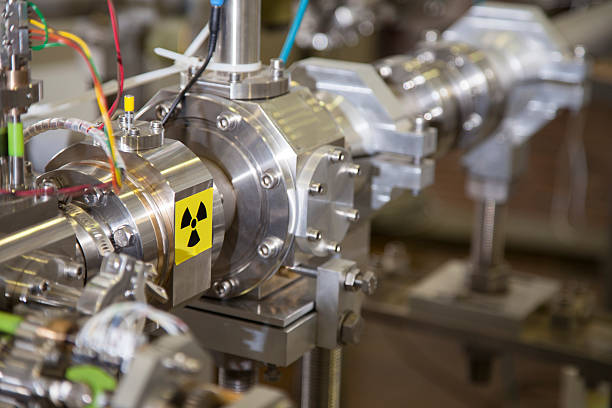
What is the Difference Between Proximity Sensors and Ultrasonic Sensors?
In the field of automation and sensing technology, proximity sensors and ultrasonic sensors are two critical components that are often confused. They both serve the purpose of detecting objects without physical contact, but their working principles, applications, and strengths vary significantly. In this article, we will break down the key differences between proximity sensors and ultrasonic sensors, explore their unique features, and discuss the advantages each offers in different settings.
Understanding Proximity Sensors
A proximity sensor is a device that detects the presence or absence of an object without making any physical contact. It is a general term for a variety of sensors that employ different working principles to achieve object detection, including electromagnetic, capacitive, or photoelectric effects. Proximity sensors are often utilized to improve automation systems by providing precise and reliable detection. They are widely used in various industries such as manufacturing, automotive, and consumer electronics.
The most common types of proximity sensors include:
Inductive Proximity Sensors: These are used mainly for detecting metallic objects. They work on the principle of electromagnetic induction, creating a magnetic field that changes when a metal object comes into proximity.
Capacitive Proximity Sensors: These sensors are versatile as they can detect both metallic and non-metallic objects, including wood, plastic, and glass. Capacitive sensors work based on changes in capacitance between the sensor and the object.
Photoelectric Proximity Sensors: These sensors use light to detect the presence of an object, making them suitable for detecting clear and colored items. They are widely used in packaging and conveyor applications.
The different types of proximity sensors make them highly flexible and useful in a wide range of applications. However, the detection range is often limited, typically not exceeding 50 mm for inductive sensors and 20 cm for capacitive sensors.
Applications of Proximity Sensors
Proximity sensors have a variety of applications across different industries:
Manufacturing Automation: Used for counting items on an assembly line, detecting machine parts, and ensuring positioning accuracy.
Automotive Systems: Employed for parking assistance, collision avoidance, and keyless entry systems.
Consumer Electronics: Integrated into smartphones for functions like screen on/off during calls.
These sensors are widely preferred because of their reliability, ruggedness, and low maintenance requirements. They play a key role in ensuring the smooth functioning of automated processes in manufacturing and other industries.
Learn more about Wenglor Inductive Sensor
Understanding Ultrasonic Sensors
An ultrasonic sensor, on the other hand, operates based on the principle of sound waves. Ultrasonic sensors emit high-frequency sound waves (beyond the range of human hearing) and measure the time taken for the sound to be reflected back from an object. The time delay allows the sensor to calculate the distance to the object.
Ultrasonic sensors are not limited to detecting only metallic objects; they can detect almost any material, including liquids, plastics, and even glass. This makes them very versatile and suitable for a broad spectrum of uses.
How Ultrasonic Sensors Work
Emission of Sound Waves: The sensor emits a pulse of ultrasonic sound.
Reflection of Waves: When the sound wave hits an object, it reflects back to the sensor.
Time Calculation: The sensor calculates the time taken for the wave to return, which allows it to determine the distance between the sensor and the object.
This detection principle allows ultrasonic sensors to measure distances with high accuracy. They can operate over relatively large distances compared to proximity sensors, with ranges of up to several meters.
Applications of Ultrasonic Sensors
Ultrasonic sensors are used in a wide range of applications, including:
Level Detection: Ultrasonic sensors are used in tanks and silos to measure liquid or granular levels.
Parking Assistance: In automotive applications, they are used to detect obstacles for parking assistance.
Industrial Automation: Employed in conveyor systems to measure distances and detect objects, even those that may not be metallic.
Ultrasonic sensors are ideal for applications requiring greater sensing distances and for detecting a wide range of materials regardless of their shape, size, or color.
Key Differences Between Proximity Sensors and Ultrasonic Sensors
While both sensors are used for object detection without physical contact, several key differences set them apart:
1. Detection Principle
Proximity Sensors: They work on electromagnetic, capacitive, or photoelectric effects. For example, inductive proximity sensors use magnetic fields to detect metal objects, while capacitive sensors use variations in capacitance.
Ultrasonic Sensors: These sensors work based on sound waves. They emit sound waves and calculate the time taken for the wave to return to determine the presence and distance of an object.
2. Materials Detected
Proximity Sensors: Inductive sensors detect only metallic objects, while capacitive and photoelectric sensors can detect a wider range of materials but have limitations regarding range and sensitivity.
Ultrasonic Sensors: These can detect nearly any material, including liquids, plastics, glass, and metals, making them more versatile in terms of materials detection.
3. Detection Range
Proximity Sensors: The detection range is relatively short. Inductive sensors typically have a range of up to 50 mm, and capacitive sensors up to 20 cm.
Ultrasonic Sensors: These have a significantly greater detection range, often up to several meters. This makes them suitable for applications where objects need to be detected from a distance.
4. Application Suitability
Proximity Sensors: Best suited for applications requiring short-range detection, especially in manufacturing and automation for position detection, counting, and safety systems.
Ultrasonic Sensors: More suitable for applications that require medium to long-range detection, such as distance measurement, obstacle avoidance, and level sensing in tanks.
Choosing the Right Sensor for Your Application
The choice between a proximity sensor and an ultrasonic sensor largely depends on the specific requirements of your application. Here are a few considerations to help decide:
Material Type: If you need to detect metallic objects only, then an inductive proximity sensor is ideal. However, if you need to detect other materials, an ultrasonic sensor or a capacitive proximity sensor would be more suitable.
Detection Range: For applications requiring long-range detection, ultrasonic sensors are generally preferred. Proximity sensors are better for shorter distances.
Environment: In environments with dust, dirt, or the presence of other metals, ultrasonic sensors may offer better performance as they are less affected by such environmental factors.
For more advanced sensing solutions, consider exploring our AVENTICS Magnetic Proximity Sensors that provide reliable performance even in demanding industrial environments.
Conclusion
Both proximity sensors and ultrasonic sensors have their unique strengths and are critical to different areas of industrial and consumer applications. Proximity sensors are ideal for situations where precise, close-range detection is necessary, particularly with metallic objects. In contrast, ultrasonic sensors provide longer-range detection and the ability to work with a wide range of materials, making them suitable for varied and complex environments.
Understanding the differences between these two types of sensors helps in making informed decisions about the most suitable sensor for a particular application. Whether you need precision at a short range or versatile, long-distance detection, choosing the right sensor ensures optimal performance and efficiency.
To explore a wide selection of proximity and ultrasonic sensors, or if you need expert guidance on selecting the right sensor for your needs, please contact us. Our team is ready to assist you in finding the perfect sensing solution for your project.
FAQs
1. What is the main difference between a proximity sensor and an ultrasonic sensor?
The main difference lies in their detection principles: proximity sensors use electromagnetic, capacitive, or photoelectric effects, while ultrasonic sensors use sound waves to detect objects.
2. Can ultrasonic sensors detect metallic and non-metallic objects?
Yes, ultrasonic sensors can detect almost any material, including metallic and non-metallic objects, making them highly versatile.
3. Which sensor is best for short-range detection?
Proximity sensors are ideal for short-range detection, particularly inductive sensors for metallic objects and capacitive sensors for other materials.
4. Are proximity sensors suitable for outdoor use?
Ultrasonic sensors are generally more suitable for outdoor use as they are less affected by environmental conditions like dust and humidity compared to proximity sensors.
5. What types of proximity sensors are available?
There are several types of proximity sensors, including inductive, capacitive, and photoelectric sensors, each with its specific use case and material compatibility.